In the mining sector, the consumable costs of enterprises often represent the largest share of total mining expenses. Addressing how to curtail these costs is a perennial challenge across the mining industry. For many years, ceramic grinding balls have served as the grinding media of choice for fine grinding processes.
These balls are typically employed in high-speed rotary equipment designed for fine grinding, such as ISA, Smith VXP, and Metso SMD grinders. The hallmark of these devices is the high velocity achieved between the grinding media, which, through differential motion, generates a grinding force that effectively processes the material.
Conversely, the vertical spiral agitating mill operates on a different principle, relying on the slow rotational movement of the spiral agitator to exert the pressing and shearing forces necessary for grinding, courtesy of the grinding media. Here, the density of the grinding media emerges as a critical factor influencing the grinding outcome.
Traditionally, the mining industry has favored high-chromium steel balls for vertical mixing grinding due to their robust hardness and commendable wear resistance. In contrast, standard ceramic balls are known for their lighter density and comparatively lower hardness.
However, recent advancements in wear-resistant material technologies have paved the way for the development of a novel nano-ceramic ball, crafted from alumina or zirconia.
advantages of ceramic grinding
Energy EfficiencyCeramic grinding media, despite its larger quantity, has a significantly lower total mass compared to other media, leading to substantial energy savings under identical grinding conditions.
Reduced Media ConsumptionEmpirical data shows that traditional medium steel balls yield a consumption rate of 0.68~0.11 kg/t.
In contrast, ceramic grinding media exhibits a much lower rate of 0.052~0.063 kg/t. Factoring in the costs—ceramic balls at 35,000 RMB/t and high chromium forged balls at 7,800 RMB/t—the switch to ceramic balls can slash production costs by approximately 65%.
Extended Lifespan of Spiral LinersThe adoption of ceramic ball media is associated with an increased lifespan for spiral liners in vertical mills.
Minimized Inspection DurationCeramic balls maintain a consistent hardness throughout and retain a spherical shape even after wear, presenting a smooth surface
Steel balls, on the other hand, due to their inconsistent hardness, wear down to irregular polygonal shapes
This characteristic ensures that ceramic balls are more readily expelled from the mill, effectively reducing inspection times.
Additionally, the lighter density of ceramic balls eases the manual removal of residual spheres post-grinding
Diminished Iron ContaminationThe presence of impurities, particularly iron, is a critical determinant of the quality of most non-metallic minerals.
Numerous non-metal grinding processes aim to minimize iron contamination, often incorporating iron removal steps during processing. Utilizing ceramic grinding media in the fine grinding phase can significantly mitigate iron impurity pollution.
For the mining industry, ceramic grinding media stands out as the optimal choice, catering to a diverse array of milling requirements.
Chemshun Ceramics has engineered a comprehensive selection of ceramic grinding media, offering the widest range of sizes and densities to accommodate both horizontal and vertical mills for fine and ultra-fine grinding, mixing, and dispersing.
Should you have any ceramic grinding media needs for the mining sector, Chemshun Ceramics welcomes your inquiries at any time.
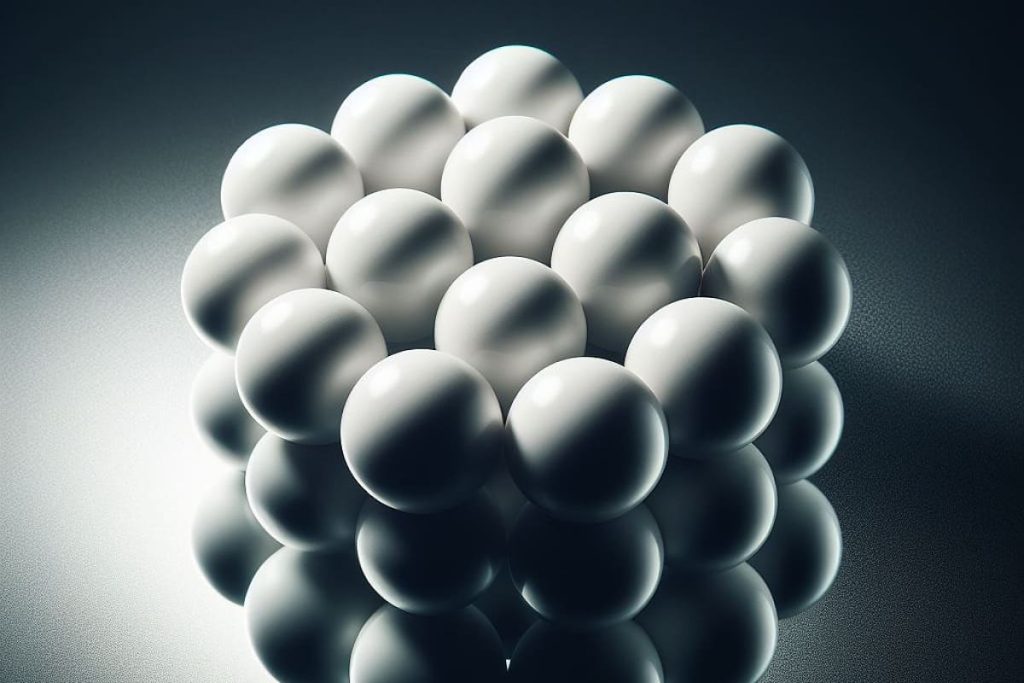
Ceramic vs. Steel Grinding Balls
Composed of materials like silicon nitride, alumina, and zirconia, ceramic balls are selected for their durability, resistance to wear, and chemical stability. They are produced through a process of high-temperature firing and precision grinding, resulting in balls with notable hardness, low density, and high resistance to temperature and corrosion.
These properties make them suitable for grinding applications where contamination must be minimal and efficiency Is key.
Steel grinding balls
Forged or rolled from various types of steel, these balls’ properties—hardness, resilience, and wear resistance—are influenced by the steel’s composition. The production process involves heating and shaping the steel into balls, then heat-treating them to obtain the desired characteristics. Known for their impact strength and heft, steel balls are Ideal for heavy-duty grinding tasks where abrasiveness and mechanical wear are prevalent.
Efficiency and Effectiveness
Ceramic balls enhance the grinding process by reducing friction and wear, leading to quicker processing and energy savings. Their inertness also prevents chemical interaction with the ground material, preserving its purity. Steel balls, with their greater density and impact strength, excel at breaking down tougher materials, essential in sectors like mining and cement production.
Wear Resistance and Durability
Ceramic balls offer superior wear resistance, prolonging their lifespan and reducing replacement frequency. This also means less contamination of ground materials, vital in industries like pharmaceuticals and food processing. Steel balls, though hardy, may wear faster in high-impact settings, potentially increasing operational costs over time.
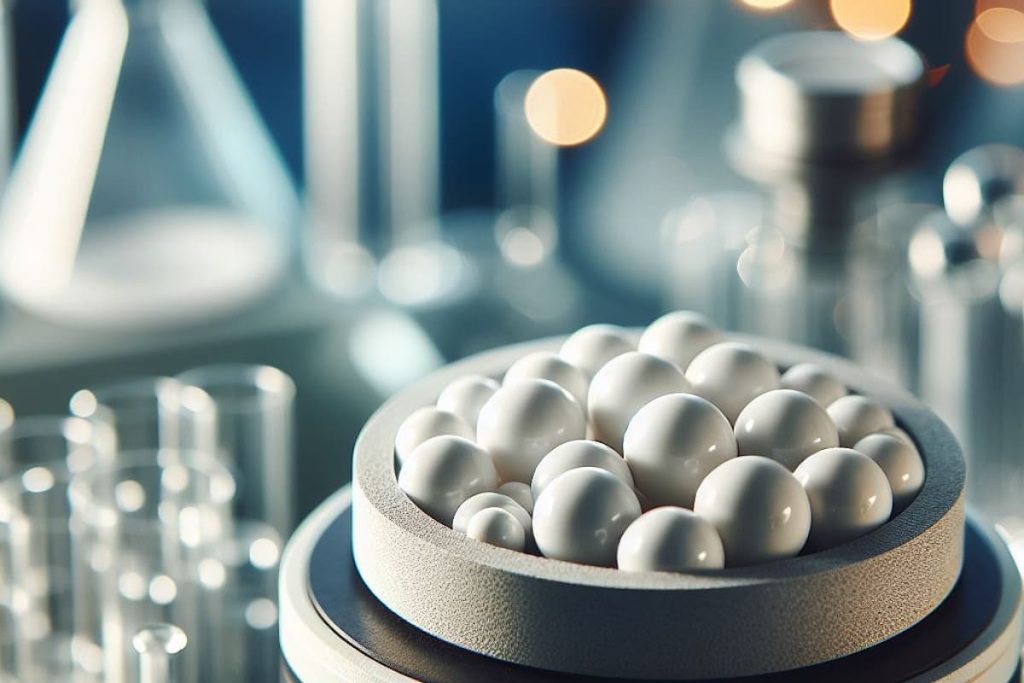
Impact on Ground Materials
The composition of grinding balls can affect the purity and traits of the ground material. Ceramic balls, being inert, eliminate contamination risks, crucial in electronics, pharmaceuticals, and food production. Steel balls might introduce metallic contamination under certain conditions, which could be undesirable in some applications
Operational Consideration
The success of grinding processes depends on the compatibility of the grinding media with the operation’s specific conditions and requirements. This requires careful consideration of the grinding types and environmental factors that could impact the performance and longevity of ceramic and steel balls
Application Suitability
Ceramic balls are favored in precision applications needing minimal contamination, like in pharmaceutical, food processing, and semiconductor industries, due to their wear resistance and inertness. Steel balls are preferred for grinding hard materials in heavy-duty operations like mining and cement production, thanks to their impact strength and durability
Environmental Factors
Grinding balls’ performance can be influenced by environmental conditions like temperature and humidity. Ceramic balls withstand a broader range of conditions, including high temperatures and corrosive environments. Steel balls may be more prone to corrosion unless treated or made from corrosion-resistant alloys.
Economic Factors
Choosing between ceramic and steel grinding balls involves considering their initial cost and long-term cost-effectiveness, including maintenance and replacement needs
Cost Analysis
Ceramic balls, though more expensive initially, may offer a lower total cost of ownership due to their durability and reduced wear rate. They require less frequent replacement, beneficial for processes where purity Is critical.
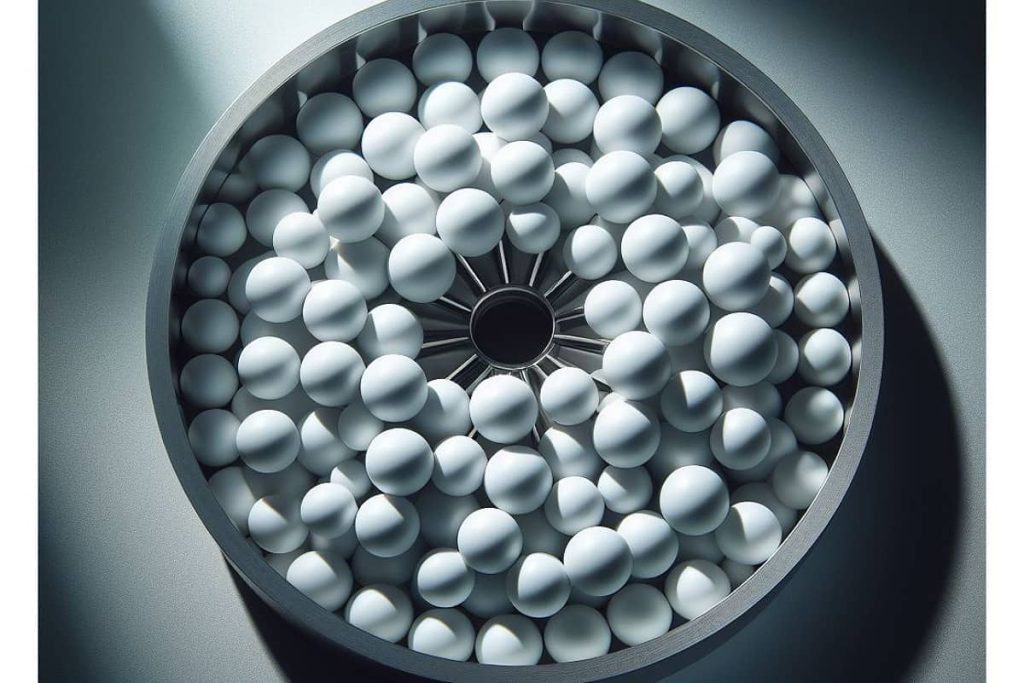
Maintenance and Replacement
Ceramic balls have lower maintenance needs, thanks to their wear and corrosion resistance, leading to less downtime and fewer replacements. Steel balls may need more frequent replacements in demanding environments, increasing maintenance costs and potential production interruptions
conclusion
When selecting between ceramic and steel grinding balls, it’s essential to consider the unique benefits each offers for certain industrial applications. Ceramic balls are the go-to for tasks that require high precision and minimal contamination, such as in the pharmaceutical and electronics sectors, due to their long-lasting nature and low potential for impurities.
Steel balls are preferred in situations that demand durability and cost-efficiency, making them a staple in rigorous activities like mining and cement production
Therefore, the decision to use ceramic or steel balls should be informed by the specific requirements of the grinding task at hand, taking into account the characteristics of the materials, the conditions of the operational environment, and the financial implications.
A thorough understanding of these elements will lead to choosing the most fitting grinding ball, which will enhance efficiency, extend the lifespan, and ensure cost-effectiveness in various industrial milling and grinding operations.
FAQ
Why should I use a ceramic grinding ball?
Composed of materials like alumina, silicon nitride, and zirconia, ceramic ball is selected for durability, resistance to wear, and chemical stability.
What is steel grinding balls?
Forged or rolled from different types of steel, these balls’ properties—hardness, resilience, and wear resistance—are influenced by the steel’s composition.
How I choose between ceramic and steel grinding balls?
When selecting between ceramic and steel grinding balls, it’s essential to consider the unique benefits each offers for certain Industrial applications..