Grinding balls are the heart of milling processes, playing a critical role in reducing materials into fine powders for industries like mining, cement, ceramics, and chemicals. The choice between wet and dry grinding balls significantly impacts efficiency, cost, and product quality. Wet grinding balls operate in a liquid medium, while dry grinding balls process materials without liquid. This guide explores the differences between wet and dry grinding balls, their applications, benefits, drawbacks, and practical strategies for selecting the right type for your milling needs.
What Are Wet and Dry Grinding Balls?
Grinding balls are spherical media used in mills (e.g., ball mills, SAG mills) to crush and grind materials through impact and attrition. They are typically made of steel, ceramic, or zirconia and vary in size from 5 mm to 150 mm, depending on the application.
- Wet Grinding Balls: Used in mills with a liquid medium (e.g., water or solvent), ideal for slurries in mineral processing, paints, or pharmaceuticals.
- Dry Grinding Balls: Used in mills without liquid, suitable for dry powders in cement production or ceramic processing.
The choice between wet and dry grinding balls depends on the material, desired particle size, and milling process.
Key Characteristics
- Material: Steel (forged or high-chrome) for durability in hard materials, ceramic or zirconia for high-purity applications.
- Size: Smaller balls (5–20 mm) for fine grinding, larger balls (50–150 mm) for coarse grinding.
- Hardness: Typically 55–65 HRC (Rockwell Hardness) for steel balls, higher for ceramic or zirconia.
- Wear Resistance: High-chrome or ceramic balls offer superior wear resistance, critical for abrasive materials.
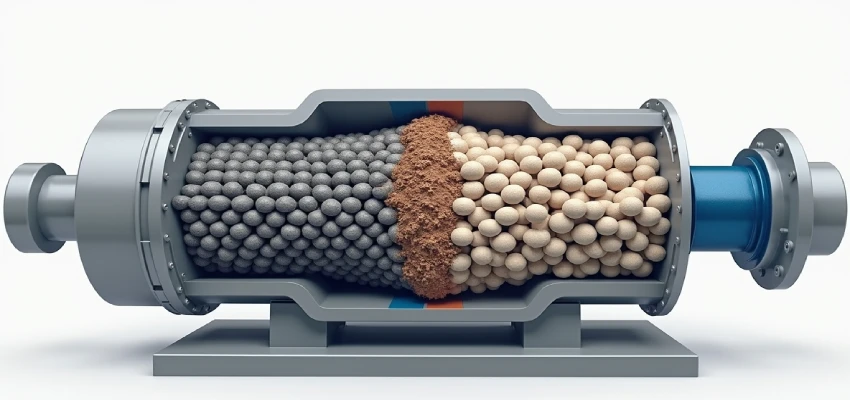
How Wet and Dry Grinding Balls Work
Both wet and dry grinding balls function by tumbling inside a rotating mill, creating impact and attrition forces to reduce particle size. However, the presence or absence of a liquid medium creates distinct operational dynamics:
Wet Grinding Balls
- Mechanism: Operate in a slurry (60–80% solids by weight), where the liquid facilitates finer grinding and reduces friction.
- Process: The liquid medium suspends particles, improving flow and enabling particle sizes down to 1–100 micrometers.
- Example: In gold mining, wet grinding balls (40–60 mm steel) process ore slurries to achieve 80% passing 75 micrometers for flotation.
Dry Grinding Balls
- Mechanism: Operate without liquid, grinding dry materials into powders through direct impact and abrasion.
- Process: Suitable for materials that don’t require a liquid medium, producing particle sizes of 50–500 micrometers.
- Example: In cement production, dry grinding balls (50–100 mm steel) grind clinker to a fineness of 3,000–4,000 cm²/g (Blaine).
Applications of Wet and Dry Grinding Balls
The choice of grinding balls depends on the industry and milling requirements:
Wet Grinding Balls
- Mineral Processing: Grinds ores (e.g., gold, copper) into fine slurries for flotation or leaching.
- Example: 50 mm forged steel balls in a wet ball mill process 500 tons/hour of copper ore slurry.
- Paints and Coatings: Produces fine pigment dispersions for smooth, vibrant finishes.
- Example: 10 mm ceramic balls grind paint slurries to 10–20 micrometers.
- Pharmaceuticals: Creates fine API suspensions for improved bioavailability.
- Example: 5 mm zirconia balls grind pharmaceutical compounds in a water-based slurry.
- Ceramics: Prepares uniform clay slurries for tiles or advanced ceramics.
- Example: 20 mm ceramic balls process clay slurries to below 50 micrometers.
Dry Grinding Balls
- Cement Production: Grinds clinker into fine powder for construction-grade cement.
- Example: 60 mm steel balls process 50 tons/hour of clinker in a dry ball mill.
- Ceramics: Produces dry powders for tiles, pottery, or advanced materials like alumina.
- Example: 30 mm ceramic balls grind silica to 100 micrometers for ceramic production.
- Chemicals: Processes dry powders for fertilizers, pigments, or catalysts.
- Example: 20 mm steel balls grind chemical compounds for uniform fertilizer powders.
- Mining: Occasionally used for dry grinding in small-scale or arid regions where water is scarce.
- Example: 80 mm steel balls grind iron ore in a dry rod mill.
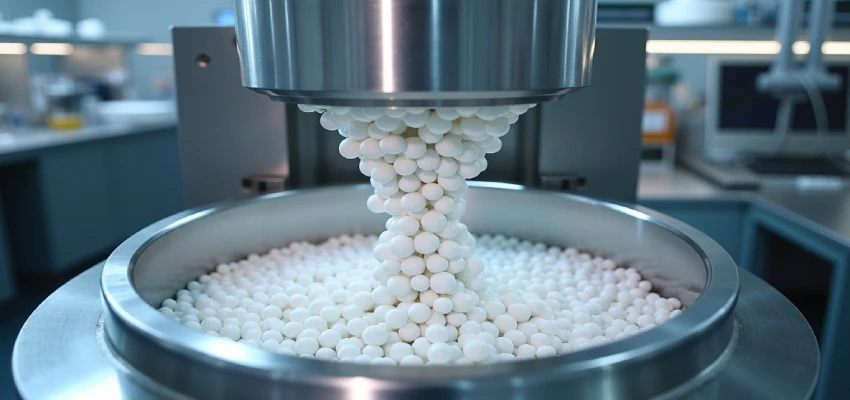
Benefits and Drawbacks of Wet and Dry Grinding Balls
Wet Grinding Balls
- Benefits:
- Finer Particle Sizes: Achieves 1–100 micrometers, ideal for high-precision applications.
- Reduced Dust: Eliminates airborne particles, improving workplace safety.
- Improved Flow: Liquid medium prevents clogging and enhances material movement.
Uniform - Dispersions: Produces homogeneous slurries for paints or pharmaceuticals.
- Drawbacks:
- Additional Processing: Requires drying steps for some applications, increasing costs.
- Corrosion Risk: Wet environments may corrode steel balls or liners unless properly treated.
- Water Usage: High water consumption can be a challenge in water-scarce regions.
Dry Grinding Balls
- Benefits:
- Simpler Process: No need for drying, reducing processing steps and costs.
- Water-Free: Ideal for arid regions or materials sensitive to moisture.
- Versatility: Suitable for a wide range of dry materials, from cement to chemicals.
- Lower Corrosion Risk: Dry environment reduces wear on steel balls and liners.
- Drawbacks:
- Larger Particle Sizes: Typically achieves 50–500 micrometers, less fine than wet grinding.
- Dust Generation: Creates airborne particles, requiring dust control systems.
- Heat Generation: Dry grinding can overheat sensitive materials, reducing quality.
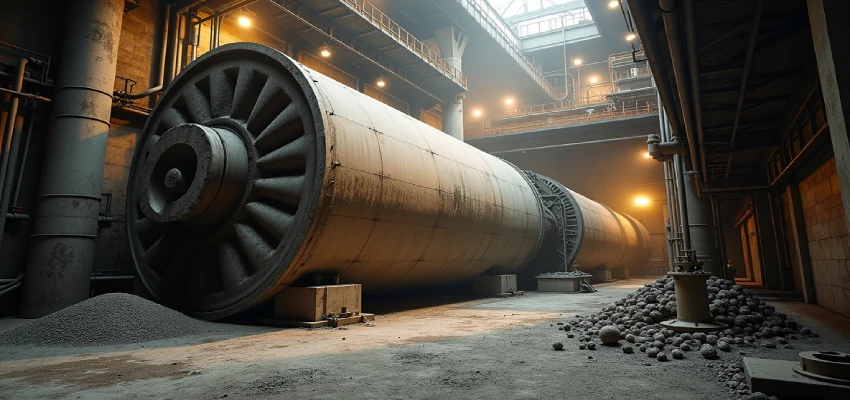
Optimizing Wet and Dry Grinding Ball Performance
To maximize the efficiency of grinding balls, consider these strategies tailored to wet and dry applications:
1. Select the Right Grinding Media
- Wet Grinding: Use ceramic or zirconia balls for high-purity applications (e.g., pharmaceuticals) and high-chrome steel for abrasive ores.
- Example: 10 mm zirconia balls for pharmaceutical slurries ensure minimal contamination.
- Dry Grinding: Use forged steel balls for hard materials like clinker, and ceramic balls for softer materials like pigments.
- Example: 50 mm forged steel balls optimize clinker grinding in cement production.
- Size: Smaller balls (5–20 mm) for fine grinding, larger balls (50–150 mm) for coarse grinding.
2. Control Mill Rotation Speed
- Wet Grinding: Operate at 60–75% of critical speed (e.g., 25–35 RPM for a 3-meter drum) to balance grinding efficiency and slurry flow.
- Dry Grinding: Operate at 65–80% of critical speed (e.g., 20–30 RPM) to ensure effective tumbling without excessive heat.
- Example: For wet gold ore grinding, 30 RPM ensures fine particles without clogging.
3. Manage Slurry Density (Wet Grinding)
- Optimal Density: Maintain 60–80% solids by weight for efficient grinding and flow.
- Adjustment: Add water or dispersants to achieve the desired viscosity (1,000–5,000 cP).
- Example: A 70% solids slurry optimizes gold ore grinding in a wet ball mill.
4. Monitor Feed Rate and Batch Size
- Wet Grinding: Use consistent feed rates (e.g., 10–20 tons/hour for industrial mills) to avoid overloading.
- Dry Grinding: Maintain steady feed rates to prevent dust buildup and ensure uniform grinding.
- Example: A dry cement mill with a 15-ton/hour feed rate achieves consistent clinker fineness.
5. Maintain Liners and Media
- Wet Grinding:
Use rubber or polyurethane liners to resist corrosion and abrasion in slurries.
- Example: Rubber liners last 1–2 years in wet ore grinding.
- Dry Grinding: Use manganese steel liners for durability with dry, abrasive materials.
- Example: Steel liners need replacement every 6–12 months for clinker grinding.
- Media Replacement:
Replenish balls every 500–1,000 hours, depending on abrasiveness.
6. Control Temperature
- Wet Grinding:
Use cooling systems to keep slurry temperatures below 50°C to protect sensitive materials.
- Dry Grinding:
Monitor heat generation and reduce speed for heat-sensitive materials. - Example: In pharmaceutical wet grinding, 30–40°C ensures API stability.
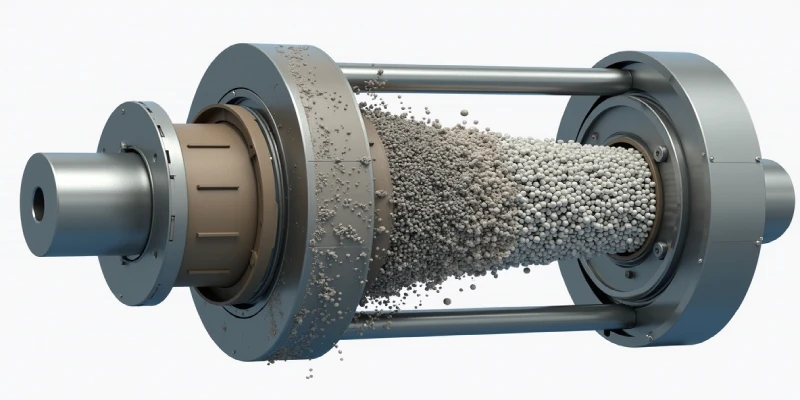
Choosing Between Wet and Dry Grinding Balls
Selecting the right grinding balls
- depends on your application: Material Type: Wet grinding for ores, pigments, or pharmaceuticals requiring fine particles; dry grinding for cement, ceramics, or water-sensitive materials.
- Particle Size: Wet grinding for 1–100 micrometers; dry grinding for 50–500 micrometers.
- Environment: Wet grinding for dust-free operations; dry grinding for water-scarce regions.
- Media Type: Ceramic or zirconia for high-purity wet grinding; forged or high-chrome steel for robust dry or wet grinding.
Alpha Grinding Media offers high-quality forged steel, high-chrome, and ceramic balls tailored for both wet and dry grinding applications.
Challenges and Solutions
Wet Grinding Balls
- Challenge: Corrosion of steel balls in wet environments.
- Solution: Use high-chrome steel or ceramic balls to minimize corrosion.
- Challenge: Clogging of discharge grates.
- Solution: Adjust slurry viscosity and use larger grate openings.
Dry Grinding Balls
- Challenge: Dust generation affecting workplace safety.
- Solution: Install dust control systems and ensure proper ventilation.
- Challenge: Overheating of materials.
- Solution: Reduce rotation speed and use intermittent grinding for sensitive materials.
Challenges and Solutions
Wet Grinding Balls
- Challenge: Corrosion of steel balls in wet environments.
- Solution: Use high-chrome steel or ceramic balls to minimize corrosion.
- Challenge: Clogging of discharge grates.
- Solution: Adjust slurry viscosity and use larger grate openings.
Dry Grinding Balls
- Challenge: Dust generation affecting workplace safety.
- Solution: Install dust control systems and ensure proper ventilation.
- Challenge: Overheating of materials.
- Solution: Reduce rotation speed and use intermittent grinding for sensitive materials.
Conclusion
Choosing between wet and dry grinding balls is a critical decision that impacts milling efficiency, product quality, and operational costs. Wet grinding balls excel in producing fine, uniform slurries for mining, paints, and pharmaceuticals, while dry grinding balls are ideal for water-free applications like cement and ceramics. By selecting the right media type, optimizing mill settings, managing slurry or feed conditions, and maintaining equipment, you can achieve superior grinding results. Understanding the differences, benefits, and optimization techniques of wet and dry grinding balls empowers you to make informed decisions for your milling processes, ensuring high performance and cost-effectiveness.
Frequently Asked Questions (FAQs)
1. What is the main difference between wet and dry grinding balls?
Wet grinding balls operate in a liquid medium, achieving finer particle sizes (1–100 micrometers) and uniform slurries, while dry grinding balls process powders without liquid, suitable for larger particle sizes (50–500 micrometers).
2. Which industries benefit most from wet grinding balls?
Wet grinding balls are ideal for mineral processing (e.g., gold, copper), paints, pharmaceuticals, and ceramics, where fine particles and uniform dispersions are critical.
3. How can I reduce wear on grinding balls?
Use high-quality media (e.g., high-chrome steel or ceramic), maintain optimal rotation speeds (60–80% of critical), and regularly inspect and replenish media every 500–1,000 hours.
4. When should I choose dry grinding balls over wet grinding balls?
Choose dry grinding balls for water-sensitive materials, arid regions, or applications like cement production where drying steps are unnecessary and larger particle sizes are acceptable.