TYPES OF BALL MILL WE CAN PROVIDE:
A ball mill machine is a type of equipment used in mining and cement industries, widely known for its high application ratio in industrial settings. Named for its internal grinding media, which are mostly spherical and come in different specifications and materials, the machine is called a ball mill.
As a professional manufacturer and supplier of ball mill machines, we offer various types of ball mills to meet customer requirements.
- According to production mode: Dry ball mill (operated without adding water) and wet ball mill.
- According to the process used: Dryer mill, superfine ball mill, open-circuit mill, closed-circuit grinding mill, etc.
- According to raw materials: Raw mill, cement ball mill, coal ball mill, steel slag ball mill, slag ball mill, quartz ball mill, aluminum ash ball mill, etc.
cylinder, end cover, bearings, and a large gear ring of ball mill machines
- Cylinder: Filled with ball mill grinding media (steel balls or steel cylpebs) ranging in diameter from 25mm to 150mm, with a loading capacity of 25%-50% of the cylinder’s effective volume.
- End cover: Positioned at both ends of the cylinder and connected to it with screws, featuring holes in the middle for easy feeding and discharging.
- Bearings: Support the cylinder, enabling it to rotate.
The ball mill’s working process occurs within the cylinder. As the ball mill grinding media inside the cylinder reaches a certain height due to the cylinder’s rotation, it falls under its self-weight, severely impacting the raw materials in the cylinder.
Simultaneously, the revolution and rotation of the grinding media generate extrusion and peeling forces between the grinding media and the cylinder body, effectively grinding the material.
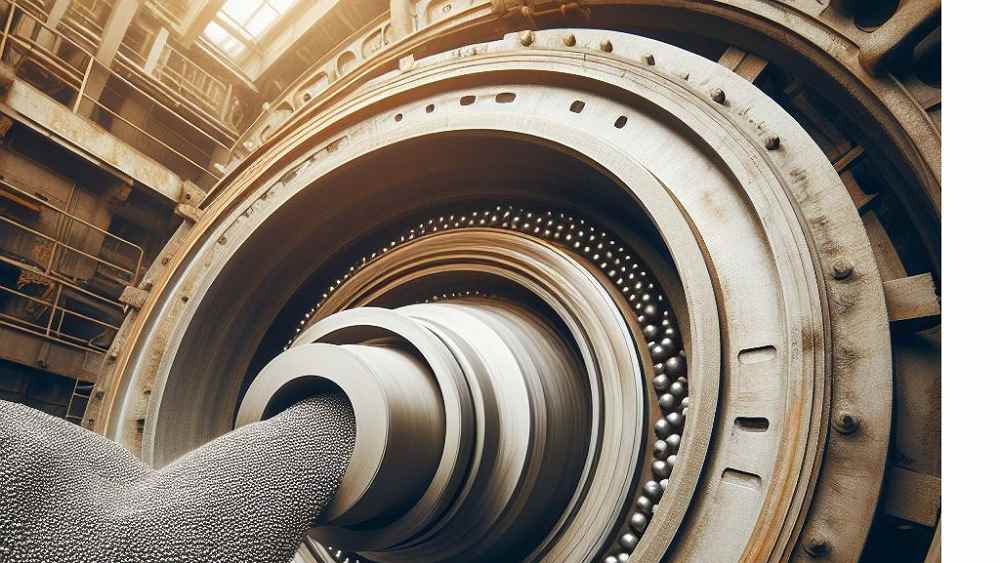
BALL MILL GRINDING MEDIA
The ball mill grinding media typically consists of spherical or small cylindrical steel cylpebs, although materials such as steel, ceramic, glass, and even rubber can be used. This variety allows the ball mill machine to grind raw materials with different properties and hardness levels.
The most common grinding medium in ball mills is spherical steel balls, often made of iron and carbon alloys, with occasional additions of chromium. Forged or cast, these steel balls boast extremely high hardness and wear resistance due to the blending of different elements.
TYPES OF BALL MILL
- Cement ball mill
- Coal ball mill
- Raw mill
- Rotary ball mill
- Tumbling ball mill
- Attritor ball mill
- Vertical ball mill
- Horizontal ball mill
- Vibration ball mill
- Conical ball mill
- Ore ball mill
- Ceramic ball mill
- Continuous ball mill
- Batch ball mill
- Grate ball mill
- Overflow ball mill
- Wet ball mill
- Dry ball mill
- Small ball mill
- Large ball mill
These types of ball mills cater to various industrial needs, offering options for both wet and dry milling processes, as well as different capacities and sizes for different applications.
Material characteristics
A diverse array of mills has been developed, each designed for specific applications. While some mills are versatile and can grind a wide variety of materials, others are tailored to meet specific grinding needs.
Material grinding is often an essential part of industrial processes, regardless of scale. In many cases, the grinding mill represents a significant investment and may be the most costly item in the operation process. Therefore, selecting a suitable grinding mill is crucial for cost-effective and trouble-free material processing, particularly when grinding is a necessary stage. It’s worth noting that most readily available hammer mills designed for agricultural grinding are unsuitable for grinding minerals.
When selecting a grinding mill, various characteristics of the material need to be taken into account. These include hardness, brittleness, toughness, abrasiveness, stickiness, softening and melting temperature, structure, specific gravity, free moisture content, chemical stability, homogeneity, and purity.
Hardness is particularly crucial, as attempting to grind a material that is too hard can lead to damage to the mill or costly maintenance requirements. For harder materials, specialized and more expensive types of grinding mills are typically employed.
Brittleness is another important characteristic to consider, indicating how easily a material breaks. While most minerals are brittle, metals tend to be ductile. However, even within minerals, there can be variations in brittleness, which impacts the grinding process.
In dry milling processes, it’s essential to keep the free moisture content of the material as low as possible to prevent issues such as material sticking to the grinding media. However, in humid regions, moisture can pose challenges, necessitating drying of the raw materials before grinding.
The final size of the material after grinding is also critical, with specific fineness requirements often stipulated. Depending on the application, a certain proportion of the material may need to be finer than a particular size threshold, typically ranging from 90% to 99%.
Grinding mills are broadly categorized into three groups: tumbling mills, roller mills, and very fine grinding mills. The latter category includes high-speed pulverizing or hammer mills, vibrating mills, pin mills, turbo mills, fluid energy mills, and stirred media mills. Each type of mill behaves differently with various materials and grinding requirements.
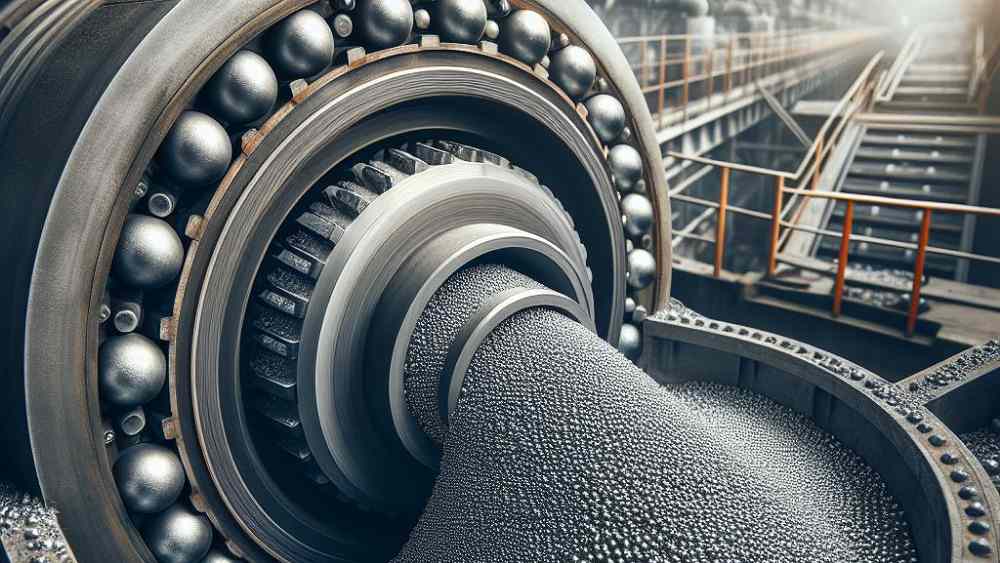
The term material grinding
In the grinding of materials, several terms are commonly used to describe different aspects of the process:
- Milling circuit: This refers to the entire system involved in the milling process, including the feed mechanism, mill, classifier, separator, and product collector. The milling circuit can be either open or closed, depending on whether there is a feedback loop for oversize particles.
- Air classification: Also known as pneumatic classification, this process involves sizing particles using a mechanical air separator.
- Batch mills: Batch mills are designed to handle a specific amount of material at a time. They grind this material and then release it before repeating the process with the next batch of material.
- Continuous mills: Unlike batch mills, continuous mills accept a continuous flow of feedstock and operate continuously. Both batch and continuous mills have their own advantages and disadvantages.
- Peripheral and trunnion discharge: This refers to the discharge of the ground product in cylindrical mills that are continuously fed. The discharge can occur either through the periphery of the mill (peripheral discharge) or through the far end of the mill (trunnion discharge).
FAQ
- What is the primary function of a ball mill in the mineral industry, and why is it extensively used?
Ball mills play a crucial role in the mineral industry by facilitating the grinding and pulverizing of ores and other materials. They are extensively used due to their ability to break particles through a combination of impact and attrition, resulting in the reduction of material size to achieve the desired product specifications.
- How are different types of ball mill designs distinguished?
Three common types of ball mill designs are identified based on their operational characteristics. The Overflow Discharge mill is suitable for fine grinding, the Diaphragm or Grate Discharge mill is preferred for additional grinding of coarse particles, and the Center-Periphery Discharge mill features dual-end feed and discharge configurations. These designs accommodate various grinding needs and particle size requirements in different industrial applications.
- What are the key components of a ball mill, and how do they contribute to its operation?
The essential components of a ball mill include the feed and discharge systems, lifters, media, liners, and the grinding chamber itself. These components work together to facilitate the grinding process by feeding materials into the mill, containing the grinding media, and providing mechanisms for particle breakage and size reduction. Proper selection and maintenance of these components are crucial for efficient mill operation.
- How do factors such as critical speed, power draw, and mill design influence ball mill operation and process control?
Critical speed and power draw are fundamental parameters that influence the design and operation of ball mills. The critical speed refers to the rotational speed at which the centrifugal force overcomes the gravitational force, leading to particle breakage. Power draw, on the other hand, reflects the energy consumption of the mill and is influenced by factors such as mill size, liner design, and ore properties. Understanding these factors allows for optimized process control and efficient operation of ball mills in various mineral processing applications.
- What are milling balls and what are they used for?
Answer: Milling balls, also known as grinding balls or milling media, are small spheres or beads made of various materials such as steel, ceramic, or glass. They are used in ball mills or attritors for the purpose of grinding, mixing, or blending materials. These balls help in reducing particle size and achieving homogeneous dispersion of substances in the milling process.
- What factors influence the effectiveness of milling balls in a ball mill?
Answer: Several factors affect the effectiveness of milling balls in a ball mill. These include the size, shape, and material composition of the balls, the speed and duration of milling, the size and hardness of the material being milled, and the presence of any additives or dispersants. Proper selection of milling balls based on these factors is crucial for achieving the desired milling results.
How do milling balls contribute to the efficiency of the milling process?
Answer: Milling balls play a critical role in the efficiency of the milling process. They facilitate the breaking down of larger particles into smaller ones through impact and attrition forces generated during milling. The uniform size and shape of the balls ensure consistent grinding action and homogenization of the milled material. Additionally, the high surface area contact between the balls and the material enhances the rate of particle size reduction and promotes efficient mixing or blending of multiple components. Overall, the proper selection and use of milling balls significantly contribute to the efficiency and effectiveness of the milling process.
- What are some common materials used to make milling balls, and what is their primary function?
Milling balls, also referred to as grinding balls or milling media, are typically crafted from materials such as steel, ceramic, or glass. Their primary function is to aid in the grinding, mixing, or blending of materials within ball mills or attritors. These balls effectively reduce particle size and promote the uniform dispersion of substances during the milling process.
- How does the size and composition of milling balls influence their performance in a ball mill?
The performance of milling balls in a ball mill is significantly influenced by their size and composition. Larger balls tend to exert greater impact forces, facilitating faster particle size reduction, while smaller balls provide more surface area for grinding and mixing. Additionally, the composition of the balls, whether steel, ceramic, or glass, affects their hardness and wear resistance, thereby impacting their durability and efficiency in the milling process. Proper selection of size and composition is crucial for achieving optimal milling results.