Ball mills are crucial equipment in various industrial processes, including material grinding, mixing, and even the production of fine powders. Their versatility and efficiency make them indispensable in industries ranging from mining and metallurgy to pharmaceuticals and chemicals. The main function of ball mills is to reduce the size of solid materials through a grinding process that involves spherical grinding media. This comprehensive guide explores the different types of ball mills, their features, applications, and the factors to consider when choosing the right ball mill for specific needs. Whether you’re involved in material processing or research, understanding the various types of ball mills will enhance your operations.
Introduction to Ball Mills
A ball mill is a cylindrical device used in grinding (or mixing) materials such as ores, chemicals, ceramics, and paints. The ball mill operates by rotating a drum filled with grinding media, which is typically made of steel, ceramic, or occasionally rubber. As the drum rotates, the grinding media collides with the material inside, gradually reducing its size. Ball mills are integral to industries that require fine particle size distributions, including mining, cement manufacturing, and pharmaceutical production. The importance of ball mills lies in their ability to efficiently process materials at a consistent size, which is critical for achieving optimal results in various industrial applications.
Different Types of Ball Mills
Horizontal Ball Mills
Horizontal ball mills are the most commonly used type in industrial applications. These mills feature a cylindrical shape and are typically mounted horizontally, with the material and grinding media moving in a rotary motion. Horizontal ball mills are widely used in mineral processing, cement manufacturing, and chemical industries. They are effective for grinding coarse materials to a finer size and are known for their simple design and ease of maintenance.
Vertical Ball Mills
In contrast to horizontal ball mills, vertical ball mills operate with a vertical orientation. These mills offer several advantages, including better energy efficiency and a compact design, making them ideal for situations where space is limited. Vertical ball mills are commonly used in applications that require fine grinding, such as in the production of inks, coatings, and pharmaceuticals. Their ability to handle finer particles makes them a preferred choice for high-quality materials.
Planetary Ball Mills
Planetary ball mills are unique in their design and function. They consist of one or more grinding jars that rotate around a central axis. The jars rotate in opposite directions, creating high energy impacts that allow for the fine grinding of materials. Planetary ball mills are typically used for laboratory applications where extremely fine materials are required, such as in the production of nanoparticles. Their main advantage is their ability to process very small amounts of material with high efficiency.
Attritor Ball Mills
Attritor ball mills are specialized mills that operate at high speeds and are used for fine grinding and dispersion of materials. Unlike traditional ball mills, attritors feature a vertical shaft with arms that agitate the grinding media and materials. These mills are particularly useful for processes that require a high degree of mixing and homogenization, such as in the production of paints, inks, and food products.
Vibratory Ball Mills
Vibratory ball mills use a unique design that applies oscillatory motion to the grinding media and material inside the mill. This motion allows for efficient grinding and is ideal for fine particles. Vibratory ball mills are commonly used in laboratory settings for the preparation of small samples, as well as in industries that require ultra-fine powder production. Their ability to work at higher speeds with smaller media makes them suitable for specialized grinding applications.
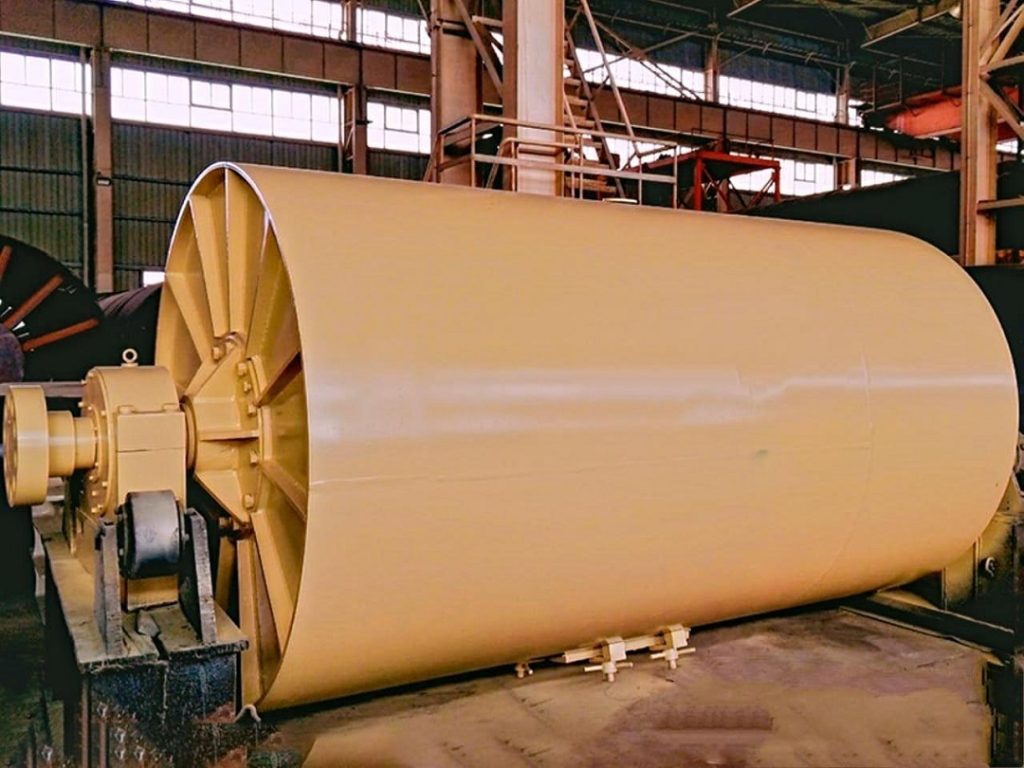
How to Choose the Right Type of Ball Mill for Your Needs
When choosing the right type of ball mill for your specific needs, several factors must be considered. These include the type of material being processed, the requirements of the grinding process, and the scale of production. For example, horizontal ball mills are ideal for large-scale operations that require heavy-duty grinding, while vertical ball mills are more suited to fine grinding applications.
Another critical consideration is the efficiency and cost-effectiveness of the ball mill. Horizontal and vertical ball mills tend to be more efficient in large-scale production, while planetary and vibratory ball mills may offer higher precision and fine grinding capabilities for smaller-scale operations. Understanding these factors will help you make an informed decision about which type of ball mill will provide the best results for your industrial needs.
Applications of Various Ball Mill Types
Different industries rely on specific types of ball mills to meet their unique processing needs. For instance, the mining industry often utilizes horizontal ball mills to handle the large volumes of material required for grinding ores. In the pharmaceutical industry, planetary ball mills are favored for their ability to grind very fine materials, which is crucial for producing high-quality powders for medications. Similarly, the ceramics industry benefits from vertical ball mills for their energy efficiency and ability to produce fine powders with minimal space. By matching the type of ball mill to the specific needs of the process, industries can maximize both efficiency and the quality of the finished product.
Advantages and Limitations of Different Ball Mill Types
Each type of ball mill has its distinct advantages and limitations. Horizontal ball mills are simple in design and maintenance but may be less efficient for fine grinding compared to other types. Vertical ball mills offer higher energy efficiency but are often more expensive and complex to maintain. Planetary ball mills provide extremely fine grinding capabilities, making them ideal for laboratory settings, but their small scale may limit their use in large production environments. Attritor and vibratory ball mills offer specialized functionality for specific applications, such as high-speed dispersion or ultra-fine grinding, but they might not be as versatile for general industrial use. Performance insights reveal that the most suitable mill type depends on the material and the desired outcome of the grinding process.
Materials Processed with Ball Mills
Ball mills are used to process a wide variety of materials, depending on the type of mill and the specific requirements of the industry. Common materials include metals, minerals, chemicals, and even foods. Horizontal and vertical ball mills are typically used for processing larger, bulk materials like ores and cement, while planetary and vibratory ball mills are more suited for fine materials such as powders and nanoparticles. The efficiency of grinding is influenced by factors such as material hardness, the size of grinding media, and the speed of the mill. Each ball mill type excels in different environments, making them versatile tools for various industries.
Maintenance and Operational Considerations
The maintenance needs for each ball mill type can vary significantly. Horizontal ball mills require regular monitoring of components such as the motor, bearings, and gears to prevent wear and tear. Vertical ball mills generally require less frequent maintenance but may need adjustments to ensure proper alignment and efficient operation. Planetary ball mills, due to their high-speed operation, need frequent inspections to prevent overheating and ensure that the grinding jars are securely fastened. For all types of ball mills, maintaining the grinding media and regularly checking for blockages or malfunctions are essential for prolonging the lifespan of the equipment. Tips for maximizing performance include using the appropriate grinding media, ensuring proper lubrication, and adhering to the manufacturer’s maintenance schedule.
Innovations and Trends in Ball Mill Technology
Ball mill technology is continually evolving, with several innovations aimed at improving efficiency and reducing operational costs. Emerging designs include more energy-efficient mills that can operate at higher speeds and with lower power consumption. Some modern ball mills also incorporate advanced monitoring systems that allow for real-time adjustments to optimize the grinding process. The future of ball mills in modern industries will likely see even greater integration with automated systems, reducing the need for manual intervention and increasing consistency across large-scale production operations. These advancements will likely make ball mills more efficient, cost-effective, and environmentally friendly.
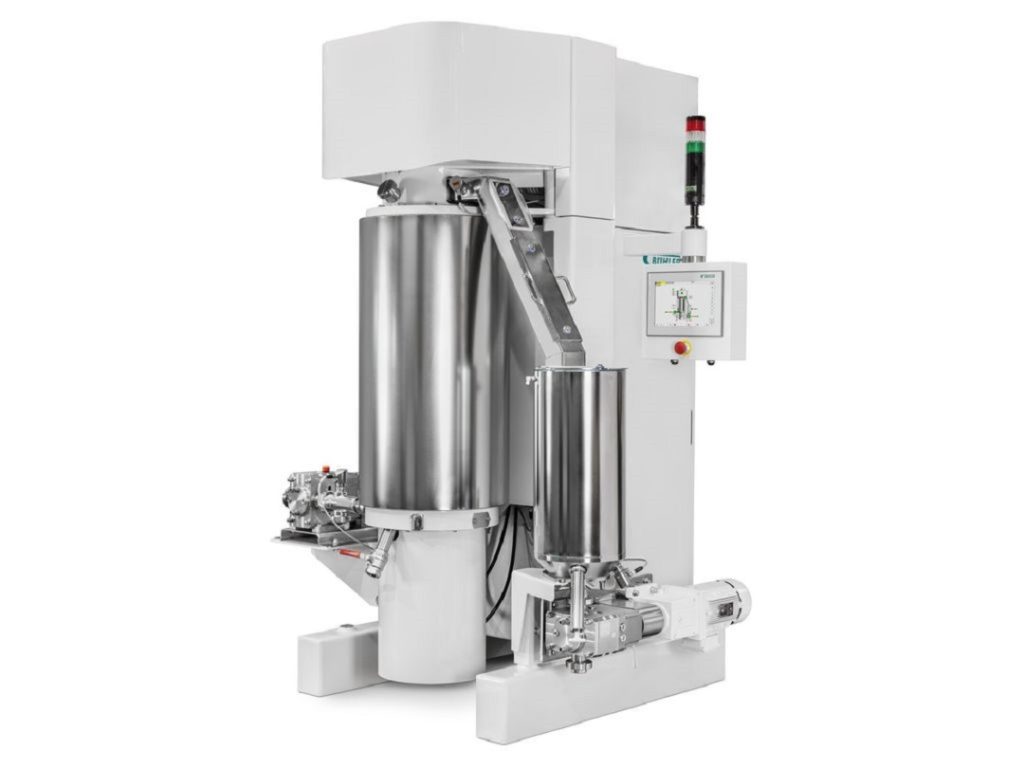
Conclusion
Choosing the right type of ball mill is crucial for achieving optimal performance in a wide range of industries. With the variety of options available, including horizontal, vertical, planetary, attritor, and vibratory ball mills, businesses can tailor their grinding processes to suit specific material needs and production goals. Alpha Grinding Media is dedicated to providing high-quality grinding media and equipment that enhance the efficiency and longevity of your ball mills. As industries continue to evolve, so too will ball mill technology, helping to shape the future of industrial processing.
Frequently Asked Questions
1. What is the primary difference between horizontal and vertical ball mills?
Horizontal ball mills are typically used for larger, bulk material grinding and are easier to maintain, while vertical ball mills are more energy-efficient and compact, making them suitable for fine grinding applications.
2. Which type of ball mill is best for laboratory applications?
Planetary ball mills are ideal for laboratory settings due to their ability to provide very fine grinding results and their suitability for small sample sizes.
3. How often should ball mills be maintained?
Maintenance frequency depends on the type of ball mill and its usage, but generally, it’s recommended to inspect the mill regularly for wear on components like the motor, bearings, and grinding media.
4. What factors affect the grinding efficiency of a ball mill?
Factors that affect grinding efficiency include the material hardness, the size and type of grinding media used, the speed of the mill, and the material’s moisture content.