The top 10 best ball mills for efficient grinding in 2024 are renowned for their performance, reliability, and innovative features. These include the Fritsch Planetary Ball Mill, Retsch High Energy Ball Mill Emax, Union Process Attritor Mill, RETSCH PM 100 Planetary Ball Mill, SPEX SamplePrep 8000M Mixer/Mill, Fritsch Pulverisette 7 Premium, RETSCH PM 200 Planetary Ball Mill, Netzsch MiniZeta, Union Process SD Series Attritors, and the Eiger Mini Motormill. Each of these mills excels in specific applications, offering superior grinding capabilities, whether for lab-scale or industrial-scale operations.
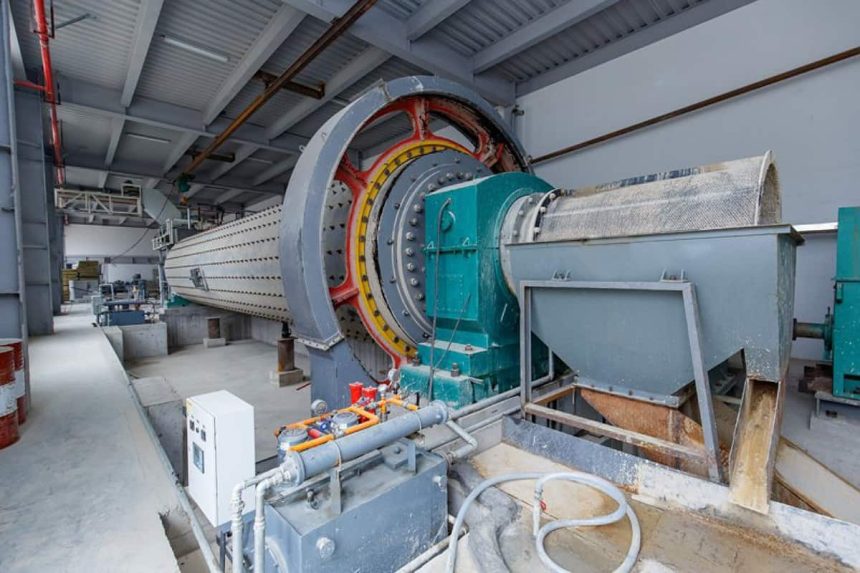
1. Cement ball mill: Used for grinding cement clinker, gypsum, limestone, and other cement raw materials.
2. Coal ball mill: Used to grind coal for power plants, including both dry and wet methods.
3. Raw mill: Used in cement production process, finely ground raw material for manufacturing cement.
4. Rotary ball mill: A type of ball mill used for fine powder making, where the shell is rotated along its axis, causing the balls to cascade and grind the material.
5. Tumbling ball mill: A versatile grinding mill that accommodates different sizes and types of grinding media, allowing mixing and grinding operations in batch or continuous applications.
6. Attritor ball mill: A type of grinder that features a cylindrical vessel rotating on its axis, typically used for small batch operations or where space is limited.
7. Vertical ball mill: Often used for working with pigments, dyes, and ceramics, this mill is characterized by its vertical orientation and ability to produce a finer product.
8. Horizontal ball mill: Commonly used for large-scale grinding operations in cement, mining, and other industrial sectors, where material is ground by impact and friction.
9. Vibration ball mill: Used for mixing and homogenizing powders in laboratories, this mill utilizes high-frequency vibration to separate particles based on their size.
10. Conical ball mill: Used to grind materials to a fine powder in pharmaceuticals, chemicals, food industries, etc., this efficient mill has conical shaped shells and rotates on its horizontal axis.
Each type of ball mill offers distinct advantages depending on its intended application, from processing large volumes of material in industrial settings to precise mixing and grinding in laboratory environments.
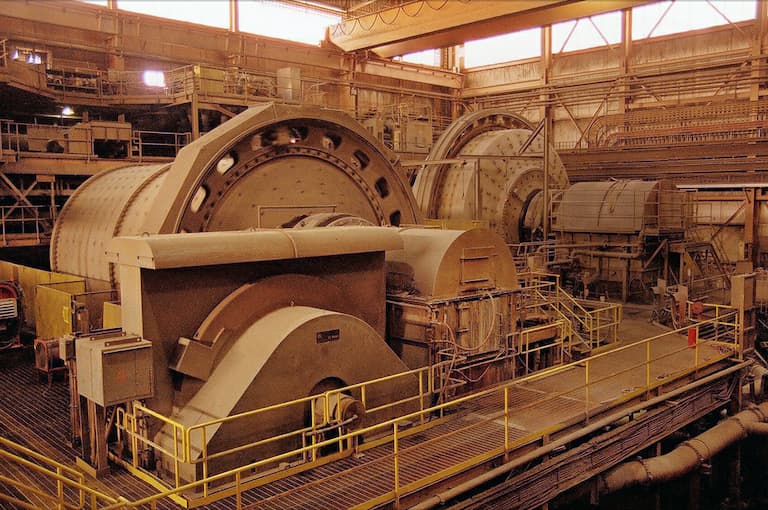
Why Choose the Best Ball Mill for Your Needs
Choosing the best ball mill for your needs is crucial for optimizing efficiency, productivity, and overall operational success in various industries. Here are several key reasons why selecting the right ball mill matters:
- Performance and Efficiency: Different ball mills are designed to achieve specific grinding goals. Whether you need fine grinding for pharmaceuticals or coarse grinding for mining, choosing a mill optimized for your application ensures efficient operation and desired particle size distribution.
- Material Compatibility: Ball mills come in various designs suited to handle different materials—from soft and brittle to hard and abrasive substances. Selecting a mill that matches the material properties (such as hardness, abrasiveness, and chemical reactivity) prevents wear and contamination issues, thereby extending equipment lifespan and maintaining product quality.
- Process Flexibility: The variety of ball mill types—such as batch, continuous, dry, wet, vertical, horizontal, and more—offers flexibility to match specific production requirements. This adaptability allows seamless integration into existing processes or customization for new applications, ensuring versatility in operations.
- Scale and Capacity: Choosing a ball mill with the right capacity and scale is essential for meeting production demands. Whether you need a small-scale laboratory mill or a large industrial-grade mill, selecting based on throughput requirements ensures optimal throughput without compromising efficiency or quality.
- Operational Costs and Maintenance: The best ball mills are designed for minimal maintenance and reduced operational costs. Features such as durable construction, efficient grinding mechanisms, and ease of maintenance contribute to lower downtime and overall operational expenses.
- Technology and Innovation: Advances in ball mill technology introduce new features like high energy input, advanced cooling systems, and precise control mechanisms. Choosing a mill that incorporates these innovations enhances performance, improves product quality, and future-proofs your investment against evolving industry standards.
- Safety and Compliance: Modern ball mills are designed with safety in mind, incorporating features like automatic shutdown mechanisms, protective enclosures, and ergonomic designs. Ensuring compliance with safety regulations and standards protects personnel and assets, fostering a safe working environment.
- Supplier Reliability and Support: Opting for reputable suppliers ensures reliable delivery, quality assurance, and ongoing support for maintenance and troubleshooting. Choosing a trusted supplier provides peace of mind and ensures long-term partnership for continuous improvement and technical support.
In conclusion, selecting the best ball mill involves assessing specific needs, considering material properties, operational requirements, and technological advancements. This strategic approach maximizes productivity, enhances product quality, and optimizes operational efficiency across various industrial applications.
Comminution Processes:
1. Crushing: This is the initial stage where large rocks or ore particles are subjected to mechanical forces to reduce their size. Jaw crushers, gyratory crushers, and cone crushers are commonly used in crushing operations.
2. Grinding: Following crushing, grinding further reduces the particle size of the material. Grinding is typically performed using ball mills and rod mills, where the grinding media (balls or rods) cascade within the mill to crush and grind the material. Grinding is usually carried out wet, enhancing efficiency and reducing wear on the grinding media.
Key Features to Look for in a Ball Mill
- When evaluating a ball mill for industrial or laboratory use, several key features are critical to consider. First, the type of grinding media compatibility—whether steel balls, ceramic balls, or others—should match your material’s properties to ensure efficient grinding and minimal wear. Second, the mill’s capacity and size should align with your production needs, balancing between batch processing and continuous operation. Third, advanced control systems and automation capabilities enhance operational efficiency and product consistency. Additionally, robust construction, easy maintenance access, and safety features contribute to reliable long-term performance.
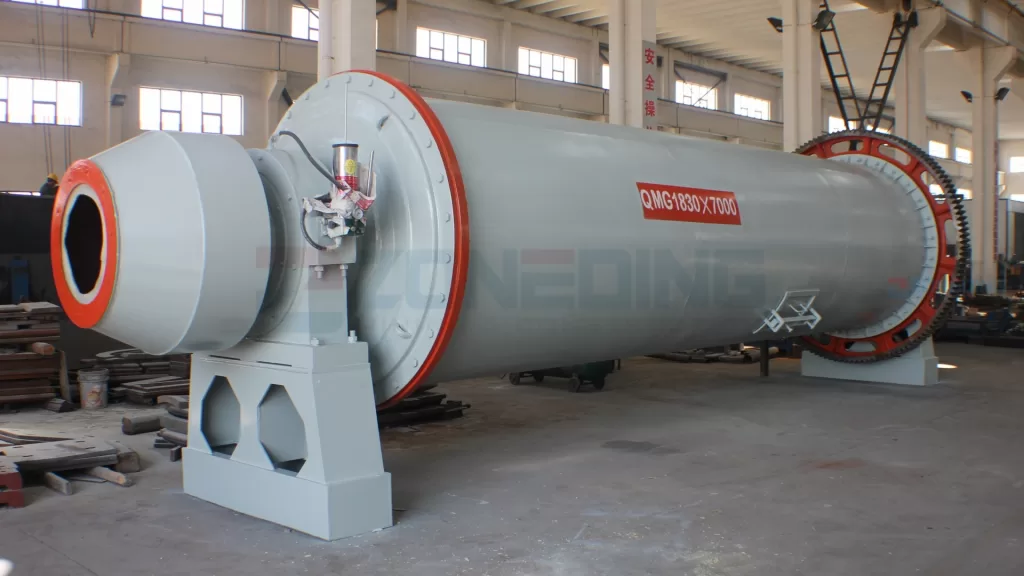
Top Ball Mill Brands and Models
The market offers a variety of reputable ball mill brands and models, each tailored to different industrial applications. Brands like Fritsch, Retsch, and Union Process are renowned for their quality and innovation in milling technology. Models such as the Fritsch Pulverisette 7 Premium planetary ball mill and the Retsch Emax high energy ball mill stand out for their advanced features and efficiency. These top brands continue to set industry standards, offering reliability, performance, and versatility across diverse sectors from pharmaceuticals to mining.
Comparing Performance and Efficiency
When comparing ball mills, performance and efficiency metrics are crucial for determining the best option for your specific needs. Factors like grinding speed, energy input, particle size distribution, and throughput capacity directly impact performance. High-energy ball mills like the Retsch Emax are designed for rapid and effective grinding of hard, brittle, and fibrous materials, while planetary ball mills excel in achieving ultra-fine particle sizes suitable for nanotechnology applications. Evaluating these metrics ensures optimal grinding efficiency and desired product quality.
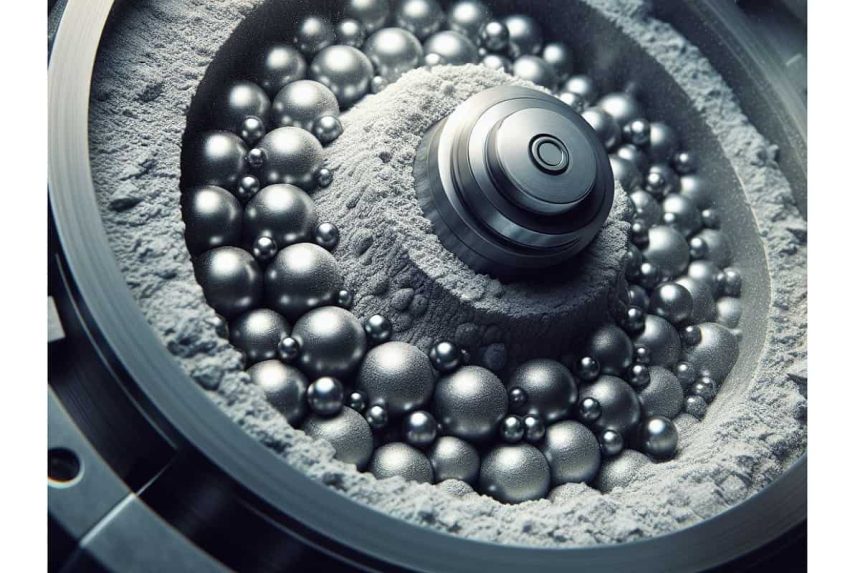
Expert Reviews and User Testimonials
Expert reviews and user testimonials provide valuable insights into the practical performance and reliability of ball mills. Experts highlight technical specifications, operational tips, and application-specific advantages that may not be apparent from technical datasheets alone. User testimonials offer firsthand accounts of real-world experiences, detailing ease of use, maintenance requirements, and overall satisfaction with specific models. Both sources contribute to informed decision-making, guiding users towards selecting the most suitable ball mill for their operational requirements and production goals.