In praise of this extraordinary element!
Iron is an incredible chemical element. On one hand, it is the most abundant element in inner and outer core of planet earth, 5% of earth core, while on the hand it is literally used in all aspects of modern life. Today several industries like electronics, construction, automotive, building, manufacturing, and even food are unimaginable without the great iron. Hematite and magnetite are the most common and favorable iron oxides in nature. Pure magnetite contains 72.4 percent iron, hematite 69.9 percent, limonite 59.8 percent, and siderite 48.2 percent, but, since these minerals never occur alone, the metal content of real ores is lower.
Let’s review the steps that are taken industry-wise to produce iron in the form of steel from earth core. The very first step is exploration which is done through magnetic survey by geologists. Then comes extraction in which iron ores that naturally happen in the core of planet earth in different forms of iron oxides, which form almost 5% of planet earth core, are extracted mechanically. Extraction itself falls into several steps like explosion.
Once extracted, ores need to become smaller and smaller in size to enable processing and purification. First size reduction step is crushing in which ores pass through 2 or 3 different jaw crushers. The resulting smaller ores are milled to even smaller particles. First in SAG mills impact forces of large grinding balls break the ores into again smaller ones and then in ball mills smaller grinding balls roll over the ores to provide finer material blend. Screening avoids any large particles in floatation. Now a ground blend of 6 to 20 mm particles is ready for floatation.
As its name suggests, depending on its design concept and applied chemicals, floatation either separates the impurities or concentrated iron in a foam layer on the surface of slurry. Floatation reagents mainly include collectors, foaming agents, and regulators and they are used to separate impurities like Sulphur.
In the next step, concentrated material goes to the so-called blast furnace where lime stone and coke are used as additives to increase furnace temperature and reduce iron oxides to iron in its elemental form. A blast furnace that is used for smelting iron ores heats up the mixture of iron ore, scrap, limestone and coke to 1600 -1920˚C resulting in molten iron and molten slag.
1 ton of iron takes approximately 1.5 – 2 tons of iron ore depending on the type of iron oxide, its concentration, impurities, etc. Although its resources are spread throughout the world, Australia and Brazil are main producers of iron ore while China is its biggest consumer. For millennia iron has been an inseparable part of human life and today this dependence is even more significant. Alongside its application in different industries, it is also the main element in grinding balls which are used to grind iron itself and other minerals.
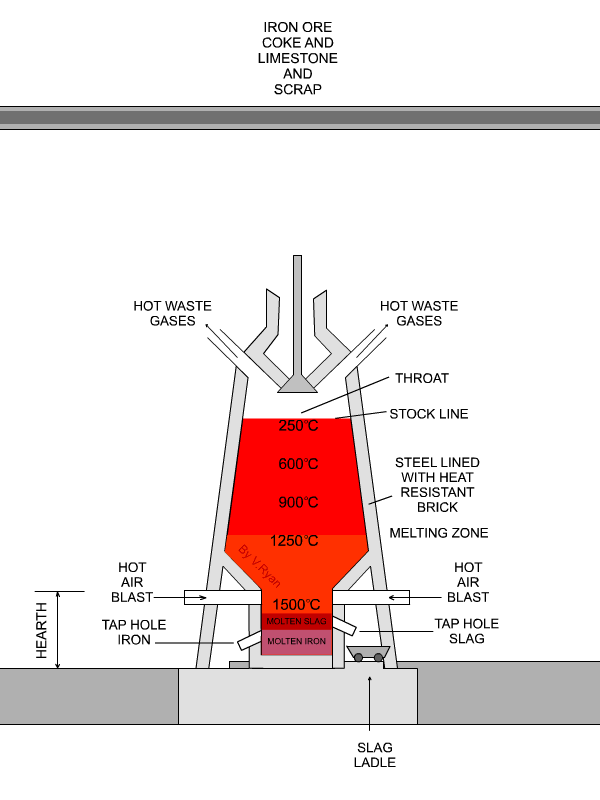