Grinding balls are essential components in various industries, particularly in mining, cement production, and power plants. These balls help in grinding materials into finer particles, ensuring optimal performance in the grinding process. However, not all grinding balls are created equal. The two primary types of grinding balls are cast grinding balls vs. forged grinding balls. The choice between these two depends on various factors, including durability, wear resistance, cost, and application requirements. This article delves into the differences between cast and forged grinding balls, their production processes, advantages, disadvantages, and applications.
Understanding Cast Grinding Balls
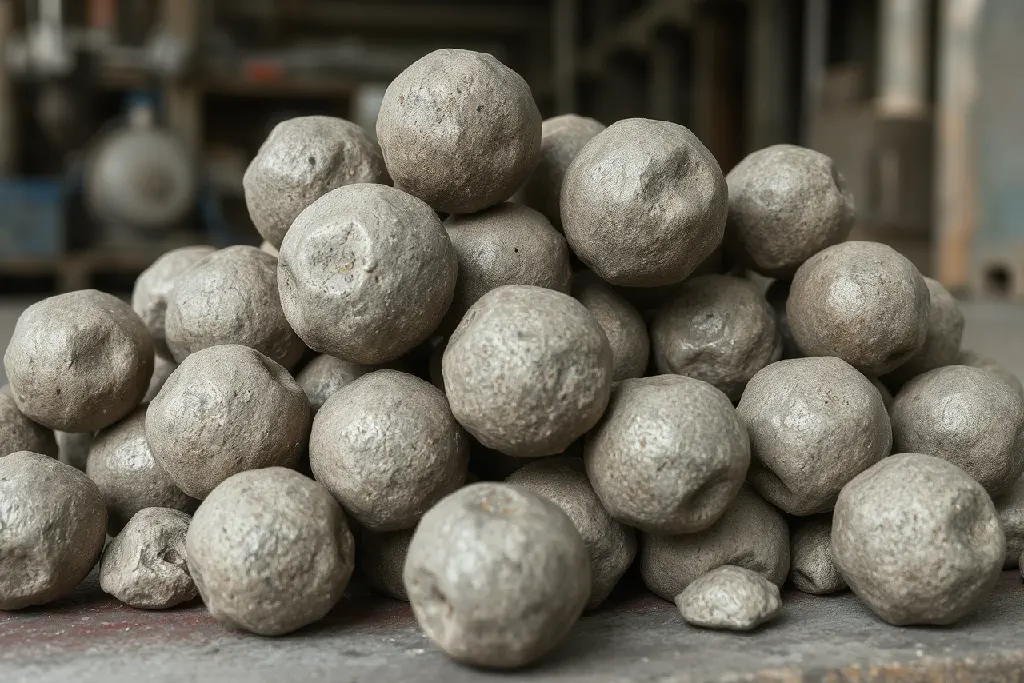
Production Process
Cast grinding balls are manufactured by melting scrap metal, pig iron, and other alloying elements in a furnace. The molten metal is then poured into molds to form grinding balls of various sizes. After casting, the balls undergo heat treatment processes such as quenching and tempering to enhance their hardness and durability.
Characteristics of Cast Grinding Balls
- Surface Hardness: Cast grinding balls typically have a higher surface hardness compared to forged ones, thanks to the heat treatment process.
- Internal Porosity: Due to the casting process, these balls may have internal defects such as porosity or shrinkage cavities, which can affect their durability.
- Brittleness: Cast grinding balls tend to be more brittle than forged balls, increasing the risk of breakage under high-impact conditions.
- Wear Resistance: The wear resistance of cast balls is generally lower compared to forged balls, especially under high-stress conditions.
Advantages of Cast Grinding Balls
- Lower Manufacturing Cost: The production process is simpler and cost-effective compared to forging.
- Consistent Hardness: Through controlled heat treatment, cast balls can achieve a uniform hardness distribution.
- Customization: Manufacturers can easily adjust the chemical composition to suit specific grinding conditions.
Disadvantages of Cast Grinding Balls
- Higher Brittleness: More prone to breaking under high impact.
- Presence of Defects: The casting process may introduce internal porosity and other imperfections.
- Shorter Lifespan: Cast grinding balls typically wear out faster than forged balls in high-impact environments.
Understanding Forged Grinding Balls
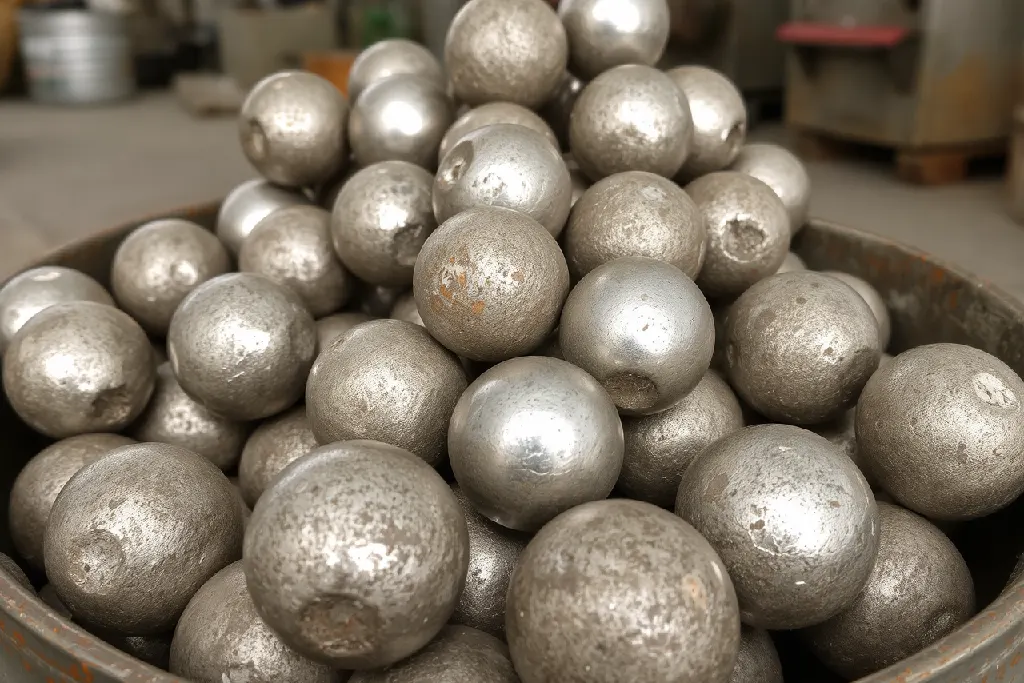
Production Process
Forged grinding balls are produced by heating a steel billet or rod to a high temperature, then using mechanical force to shape it into a spherical form. The balls are then heat-treated to achieve the desired hardness and strength.
Characteristics of Forged Grinding Balls
- Higher Toughness: Forged grinding balls exhibit greater toughness, reducing the likelihood of breakage.
- Finer Grain Structure: The forging process refines the grain structure, improving mechanical properties.
- Lower Porosity: Unlike cast balls, forged balls have minimal porosity, making them more durable.
- Better Wear Resistance: Due to their high toughness, forged grinding balls wear out more slowly than cast balls.
Advantages of Forged Grinding Balls
- Higher Impact Resistance: Less likely to break under heavy loads.
- Longer Service Life: Forged balls last longer in grinding operations.
- Better Structural Integrity: The absence of porosity improves overall strength and durability.
Disadvantages of Forged Grinding Balls
- Higher Manufacturing Cost: The forging process requires specialized equipment and more energy.
- Hardness Variability: Some forged balls may have a less uniform hardness distribution compared to cast balls.
Differences Between Cast and Forged Grinding Balls
Feature |
Cast Grinding Balls |
Forged Grinding Balls |
Production Process |
Casting molten metal into molds |
Heating and hammering metal into shape |
Hardness |
Generally higher surface hardness |
More uniform hardness distribution |
Toughness |
More brittle |
Higher toughness, less likely to break |
Porosity |
May contain internal porosity |
Minimal or no porosity |
Wear Resistance |
Moderate |
Higher, leading to longer lifespan |
Cost |
Lower |
Higher due to energy-intensive process |
Application |
Suitable for lower-impact grinding |
Ideal for high-impact environments |
Applications of Cast and Forged Grinding Balls
When to Use Cast Grinding Balls
- Cement Plants: Due to lower impact loads, cast grinding balls are often used in cement mills.
- Coal Mills: Where grinding occurs under relatively mild conditions.
- Chemical Industry: Where precise chemical composition is required.
When to Use Forged Grinding Balls
- Mining Industry: High-impact grinding in mineral processing benefits from the toughness of forged balls.
- Power Plants: Used in coal grinding applications where durability is crucial.
- Ball Mills in Hard Rock Mining: Forged balls provide better performance in environments with significant mechanical stress.
When deciding between cast grinding balls vs. forged grinding balls, several factors must be considered, including cost, application, and desired durability. The differences between cast and forged grinding balls include variations in manufacturing processes, hardness, porosity, and impact resistance. While cast balls offer a lower-cost solution with consistent hardness, forged balls provide superior toughness and wear resistance, making them ideal for demanding applications such as mining and power generation. Understanding these key differences ensures optimal grinding efficiency and cost-effectiveness in industrial applications.
Conclusion
Understanding the differences of cast and forged grinding ball is crucial for selecting the most suitable option for various industrial applications. While cast grinding balls offer cost efficiency and are ideal for specific environments, forged grinding balls provide superior strength, durability, and impact resistance, making them the preferred choice for heavy-duty operations. The differences cast and forged grinding ball influence factors such as wear resistance, toughness, and overall performance in grinding processes. To learn more about these differences and find high-quality grinding media solutions, visit Alpha Grinding Media.
FAQs
1. What are the main differences between cast and forged grinding balls?
The primary differences of cast and forged grinding ball lie in their manufacturing process and mechanical properties. Cast grinding balls are made by pouring molten metal into molds, resulting in a harder but more brittle structure, whereas forged grinding balls are shaped under high pressure, providing greater toughness and impact resistance.
2. Which industries commonly use cast and forged grinding balls?
Cast grinding balls are typically used in cement plants and low-impact mining operations due to their cost-effectiveness. Forged grinding balls, on the other hand, are preferred in mining, power plants, and heavy-duty grinding applications where high strength and durability are essential.
3. How does wear resistance differ between cast and forged grinding balls?
Forged grinding balls generally offer better wear resistance due to their refined grain structure and high impact toughness. Cast grinding balls, while harder, may wear out faster in high-impact environments due to their inherent brittleness.
4. Where can I find high-quality cast and forged grinding balls?
For premium-quality grinding media solutions and expert advice on the differences cast and forged grinding ball, you can explore Alpha Grinding Media, a trusted supplier offering a wide range of grinding products tailored to various industrial needs.