Ceramic balls are precisely engineered spherical components made from advanced ceramic materials. These balls are widely used across various industries thanks to their exceptional performance characteristics such as high hardness, low weight, thermal resistance, and chemical stability. If you’re considering purchasing ceramic balls or simply want to understand their properties and applications, read on to make a more informed and smart buying decision.
What Are Ceramic Balls?
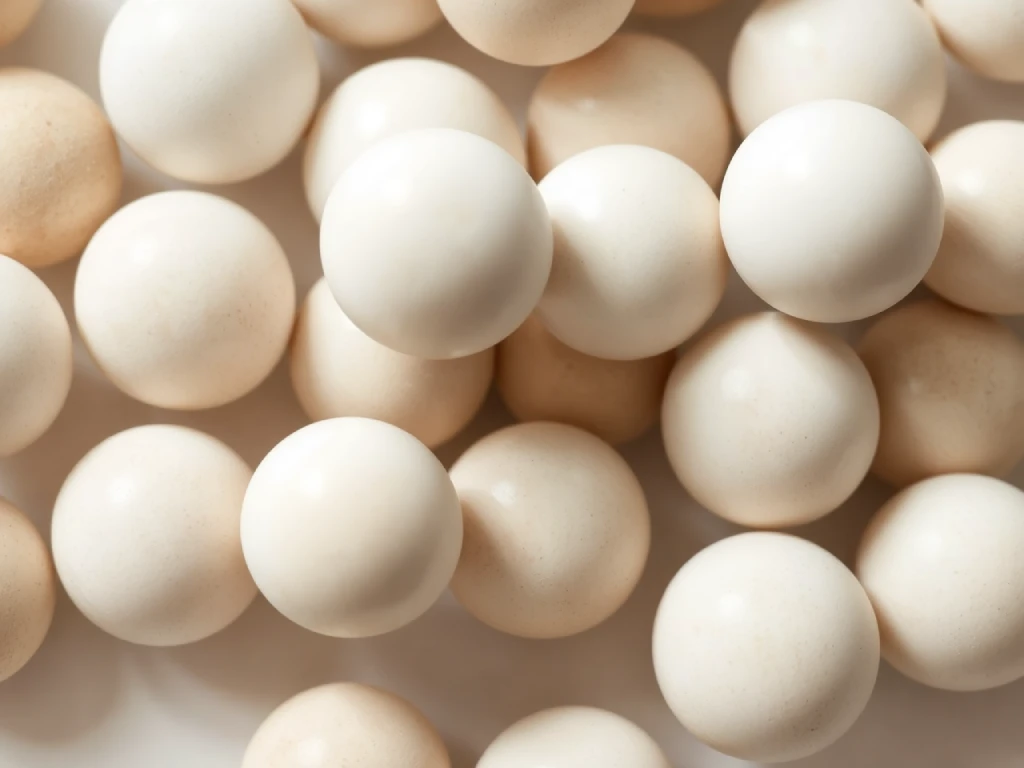
As the name suggests, ceramic balls are spherical elements manufactured from ceramic materials rather than traditional metal alloys. Depending on their intended use, ceramic balls are made in different grades and compositions to suit a variety of industrial applications.
Types of Ceramic Balls
Among the many types of ceramic balls, the two most commonly used in technical and industrial settings are:
- Alumina Ceramic Balls (Aluminum Oxide or Al₂O₃)
- Silicon Nitride Ceramic Balls
What Is Alumina Ceramic?
Alumina (Aluminum Oxide or Al₂O₃) is one of the most widely used advanced ceramic materials due to its excellent electrical insulation properties, extremely high hardness, and superior resistance to wear and corrosion. With a melting point of 2072°C, Alumina ceramics are suitable for demanding high-temperature environments. Due to their toughness, these ceramics can only be shaped through diamond grinding processes.
Key Features of Ceramic Balls
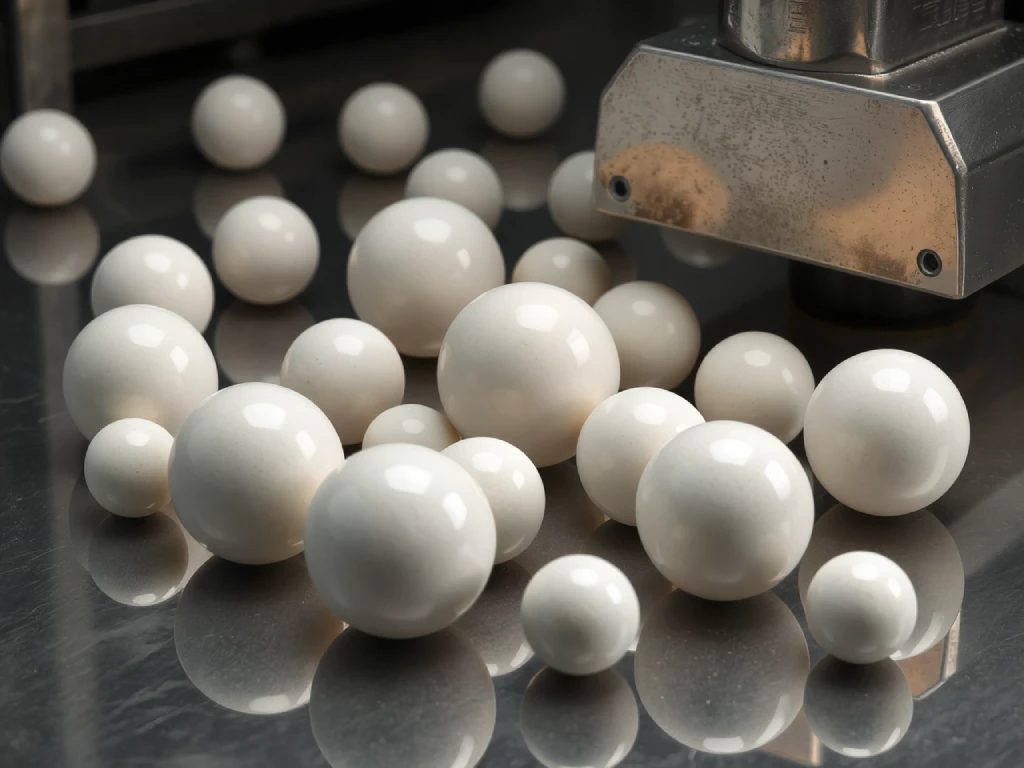
Ceramic balls possess a unique set of attributes that make them highly desirable for use in critical components. Below are some of the most important features:
1. High Hardness
Ceramic balls, especially those made from alumina or silicon nitride, exhibit significantly higher hardness than their metallic counterparts. This results in superior wear and abrasion resistance, making them ideal for high-stress environments such as bearing systems.
2. Lightweight
Ceramic materials are lighter than most metals. This reduced weight helps in minimizing the overall mass of mechanical assemblies, reducing inertia and improving energy efficiency in rotating systems.
3. High-Temperature Resistance
Ceramic balls can maintain their structural integrity and performance in extreme temperatures. This makes them highly suitable for high-heat environments like turbines, furnaces, and heat exchangers.
4. Excellent Corrosion Resistance
Due to their inert chemical properties, ceramic balls are resistant to most acids, alkalis, and corrosive agents. This feature is especially beneficial in medical, chemical processing, and food-grade applications.
5. Low Friction Coefficient
Ceramic balls offer reduced friction compared to metal balls, leading to increased efficiency and lifespan of mechanical systems like bearings, gearboxes, and motor assemblies.
6. Electrical Insulation
Unlike metal balls, ceramic balls are non-conductive and can serve as electrical insulators. This makes them ideal for applications where electrical conductivity is undesirable, such as in electric motors or sensors.
Applications of Ceramic Balls
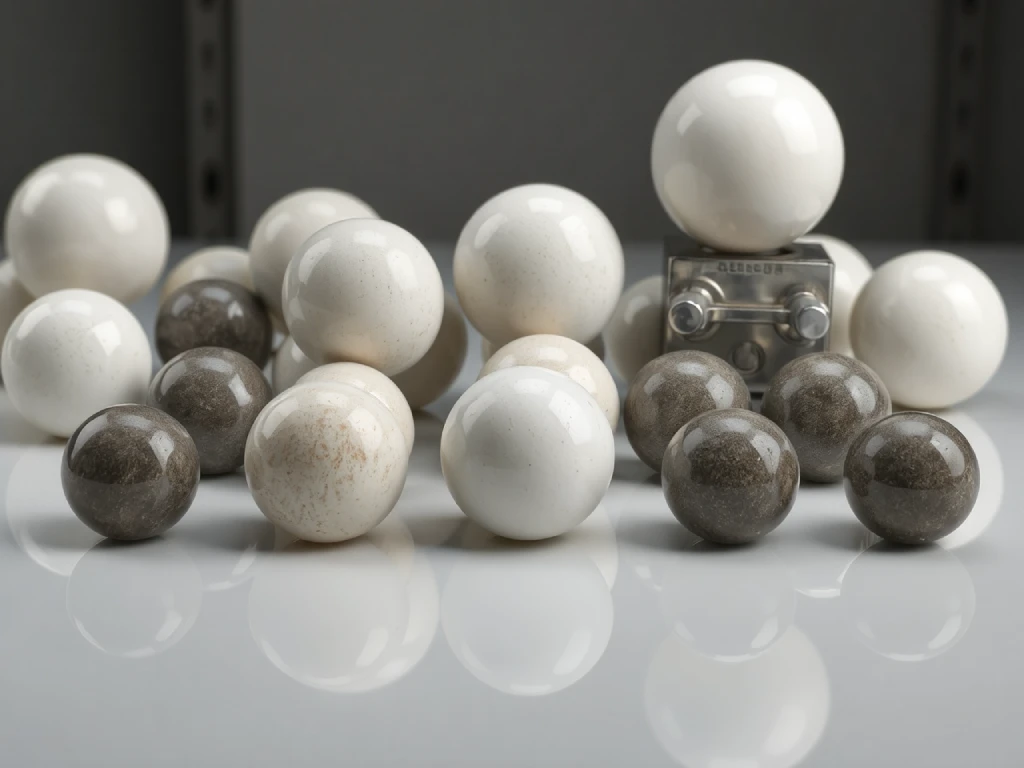
Ceramic balls are used in a wide array of industries due to their outstanding properties. Some of the key sectors include:
- Automotive Industry – Used in high-performance bearings and engine components.
- Medical Sector – Applied in surgical tools, implants, and lab equipment.
- Military and Defense – Used in precision weaponry and advanced machinery.
- Aerospace Industry – Preferred for their lightweight and high-temperature performance in jet engines and control systems.
- Industrial Machinery – Utilized in pumps, valves, and rotating equipment.
Comparison Table: Features and Applications of Ceramic Balls
Feature | Description | Application |
High Hardness | Greater wear resistance compared to metal balls | Bearings, mechanical joints |
Lightweight | Lighter than steel, reduces overall weight of the system | Automotive suspension systems |
Heat Resistance | Maintains performance under extreme temperatures | Turbines, thermal processing systems |
Chemical Resistance | Unaffected by corrosive substances | Medical and chemical industries |
Low Friction | Reduces mechanical wear and increases system efficiency | Gears, rotating parts |
Electrical Insulation | Non-conductive properties for electrical safety | Electric motors, electronic assemblies |
Benefits of Using Ceramic Balls
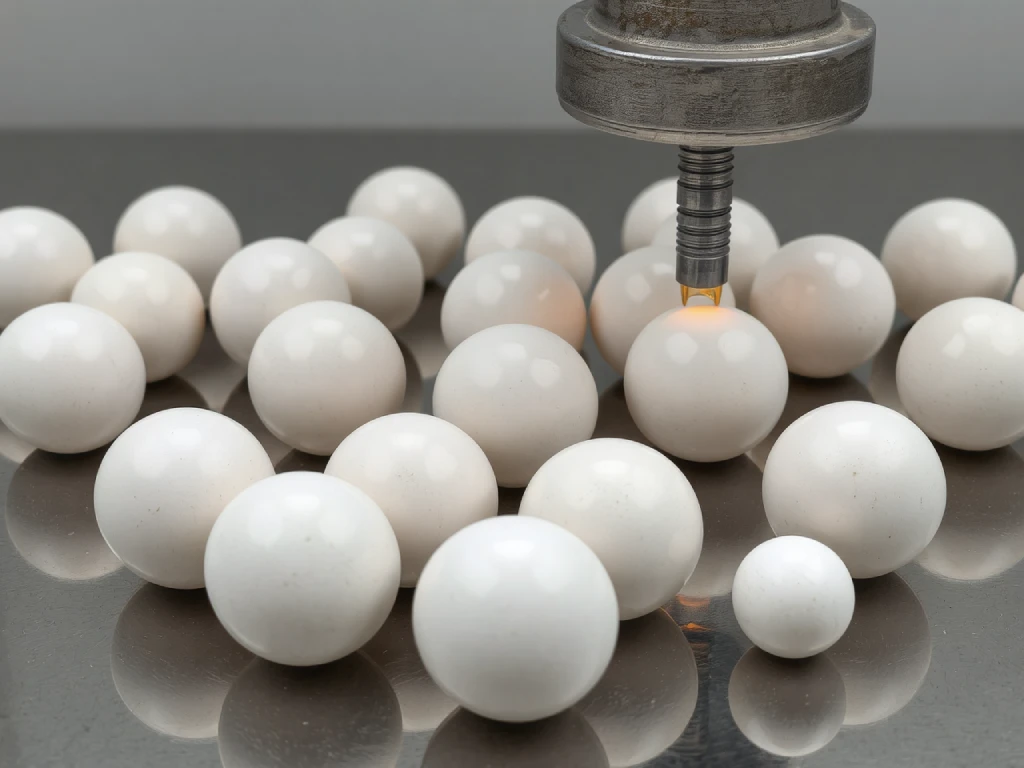
Beyond their impressive material properties, ceramic balls offer practical benefits such as:
- Longer Equipment Lifespan – Reduced wear leads to longer service intervals.
- Lower Maintenance Costs – Less frequent replacements reduce overall costs.
- Enhanced System Efficiency – Lower friction and lighter weight boost performance.
- Operational Reliability – Excellent stability under varying environmental conditions.
These advantages make ceramic balls a reliable and cost-effective choice for engineers and technical professionals looking to optimize system performance while minimizing downtime.
Ceramic Ball Prices
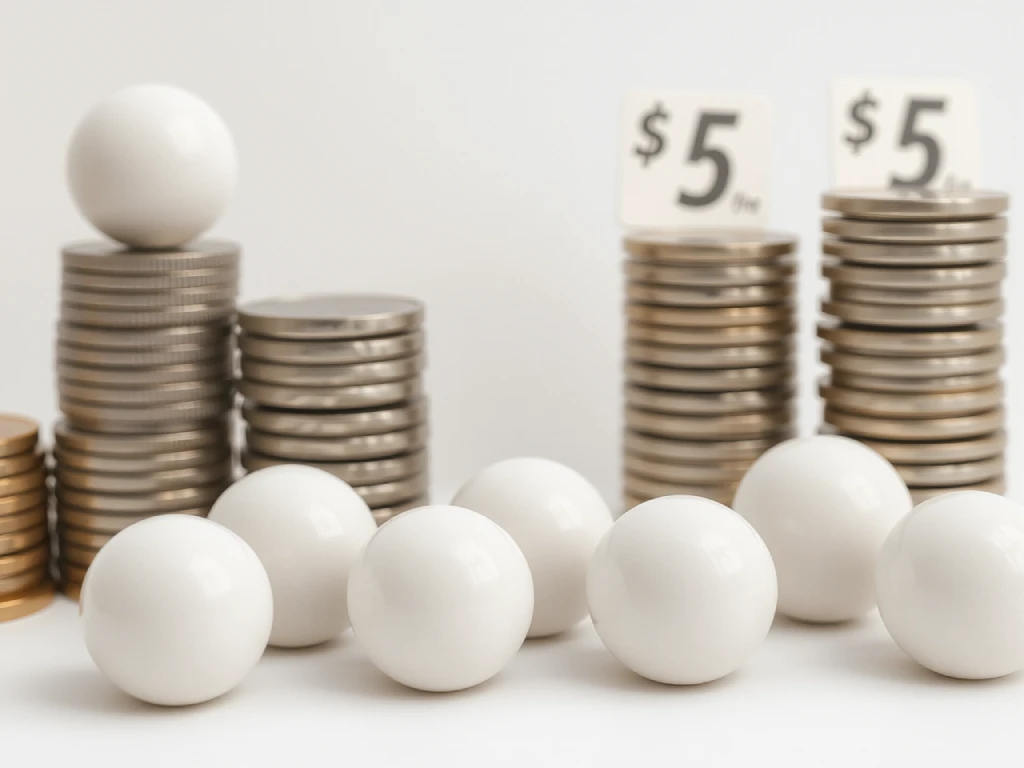
The cost of ceramic balls can vary significantly based on factors such as material composition, size, precision grade, and intended application. While they may have a higher upfront cost compared to traditional steel balls, their durability and low maintenance requirements often make them more economical over the long term.
Choosing the Right Supplier
When purchasing ceramic balls, it’s crucial to consider not only price and specifications but also the credibility of the supplier. A trusted manufacturer or distributor should offer high-quality products, technical support, and post-sales services to ensure a successful integration into your system.
Conclusion
Ceramic balls—particularly those made of alumina or silicon nitride—offer a compelling combination of strength, resilience, and versatility. Whether you’re in aerospace, automotive, medical, or industrial manufacturing, investing in high-performance ceramic balls can yield significant benefits. For expert advice and access to premium-grade ceramic balls, trust Alpha Grinding Media as your go-to source.
Frequently Asked Questions
1. What are ceramic balls made of, and how do they differ from metal balls?
Ceramic balls are typically made from advanced ceramic materials such as Alumina (Al₂O₃) or Silicon Nitride (Si₃N₄). These materials provide high hardness, excellent wear resistance, and exceptional thermal and chemical stability. Unlike metal balls, ceramic balls are non-metallic, non-magnetic, electrically insulating, and significantly lighter. Their lower density reduces rotational inertia in high-speed applications, leading to smoother and more efficient performance.
2. What are the main advantages of using ceramic balls in industrial applications?
Ceramic balls offer several key advantages:
- High hardness and wear resistance, ensuring long service life in demanding environments.
- Low friction coefficient, reducing heat and energy loss in mechanical systems.
- Corrosion and chemical resistance, making them ideal for use in harsh chemical or medical environments.
- Lightweight, decreasing mechanical load and improving speed and efficiency.
- Electrical insulation, suitable for applications where conductivity must be minimized, such as in electric motors and electronic devices.
3. In which industries are ceramic balls most commonly used?
Ceramic balls are used across a wide range of industries, including:
- Automotive: in hybrid and electric vehicle components such as turbochargers and bearings.
- Aerospace: in high-speed and high-temperature systems like jet engines.
- Medical: in surgical tools, dental devices, and prosthetics due to their biocompatibility.
- Chemical and Pharmaceutical: in processing equipment exposed to corrosive substances.
- Industrial Machinery: in high-performance bearings, valves, and grinding media.
4. How do I choose the right type of ceramic ball for my application?
Choosing the right ceramic ball depends on several factors:
- Material properties: Alumina is cost-effective and offers good wear resistance, while Silicon Nitride provides higher strength, lower weight, and superior thermal shock resistance.
- Operating environment: Consider temperature, presence of corrosive substances, and mechanical loads.
- Application type: For high-speed bearings, Silicon Nitride is usually preferred. For general chemical resistance, Alumina may be sufficient.
- Precision and size: Depending on the required tolerance and functionality, ceramic balls are available in different grades and sizes.
Consulting with a reputable supplier can help you assess these factors and choose the most suitable option for your specific application.