Ball mills are essential equipment in various industries, particularly in the fields of mining, cement, and chemical processing. These machines are used for grinding materials into fine powder, which is vital for the production of various products. Despite their reliability, ball mills can encounter several operational issues that can disrupt production processes. Understanding how to identify and resolve these issues is crucial for maintaining efficiency and prolonging the lifespan of the equipment. In this guide, we will explore the most common problems faced by ball mills, their potential causes, and effective troubleshooting solutions to keep them operating at peak performance. Whether you are dealing with a malfunctioning mill or looking to prevent future issues, this comprehensive guide provides valuable insights into the proper maintenance and repair procedures for ball mills.
1. Low Grinding Efficiency
One of the most common problems faced by ball mills is low grinding efficiency. This issue can significantly impact production rates and the quality of the final product. There are several potential causes for low efficiency, including:
- Clogged Feed Material: If the feed material contains excessive moisture or fines, it can clog the mill’s feed system, resulting in inefficient grinding.
- Incorrect Ball Size: Using incorrect ball sizes can affect the milling process. If the balls are too large or too small, they may not provide optimal grinding.
- Improper Mill Speed: Operating the ball mill at an incorrect speed can result in poor grinding efficiency. Too slow or too fast speeds can disrupt the grinding process.
Solution: To resolve low grinding efficiency, ensure that the feed material is clean and dry. Adjust the ball size to match the specific requirements of the material being processed. Regularly monitor the mill speed and adjust it to the optimal level for the type of material and desired output.
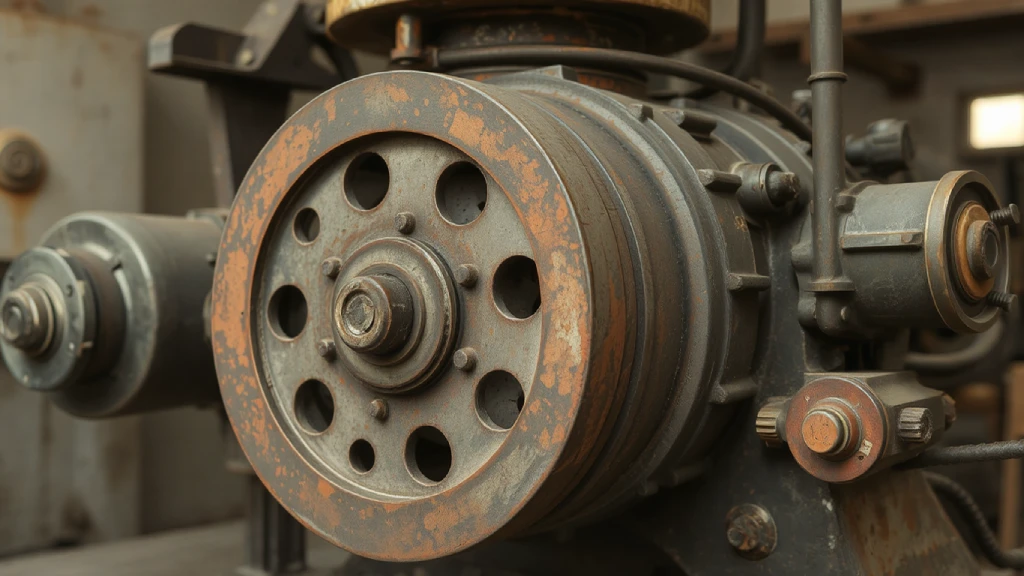
2. Overheating of the Ball Mill
Overheating is another common issue that can cause significant damage to the ball mill’s internal components. It can be caused by excessive load, poor ventilation, or friction between the grinding media and the mill shell.
Solution: To prevent overheating, ensure that the mill is not overloaded and that proper lubrication is provided to the bearings and other moving parts. Adequate ventilation and cooling systems should be in place to dissipate heat generated during the grinding process. Regularly check the condition of the lubrication system and replace any worn-out parts.
3. Excessive Noise or Vibration
Unusual noises or excessive vibrations during operation can indicate several issues, such as worn-out bearings, misalignment of components, or an imbalance in the grinding media.
Solution: If noise or vibration is detected, immediately shut down the mill and inspect the internal components. Check for any signs of wear or damage in the bearings and replace them if necessary. Ensure that all components are properly aligned, and the grinding media is evenly distributed. Balancing the mill and ensuring that all parts are functioning correctly can help resolve these issues.
4. Uneven Wear of Grinding Media
Uneven wear of the grinding media can result in inefficient grinding and increased wear on the mill’s internal components. This problem can be caused by improper ball distribution, incorrect ball size, or poor material feed.
Solution: Regularly inspect the grinding media for signs of uneven wear and replace any damaged or excessively worn balls. Ensure that the balls are evenly distributed inside the mill to prevent uneven wear. Adjust the ball size according to the material being processed and the mill’s operational requirements.
5. Mill Jamming or Blockage
Jamming or blockage of the ball mill can occur due to the accumulation of materials, improper mill speed, or inadequate feeding of the material. Blockages can cause a complete halt to operations, leading to costly downtime.
Solution: To prevent jamming, regularly clean the mill and inspect the feeding system to ensure it is functioning properly. Avoid overloading the mill with excessive material. Monitor the material flow rate and adjust it as needed to maintain smooth operation. If a blockage occurs, stop the mill immediately and clear the obstruction before restarting.
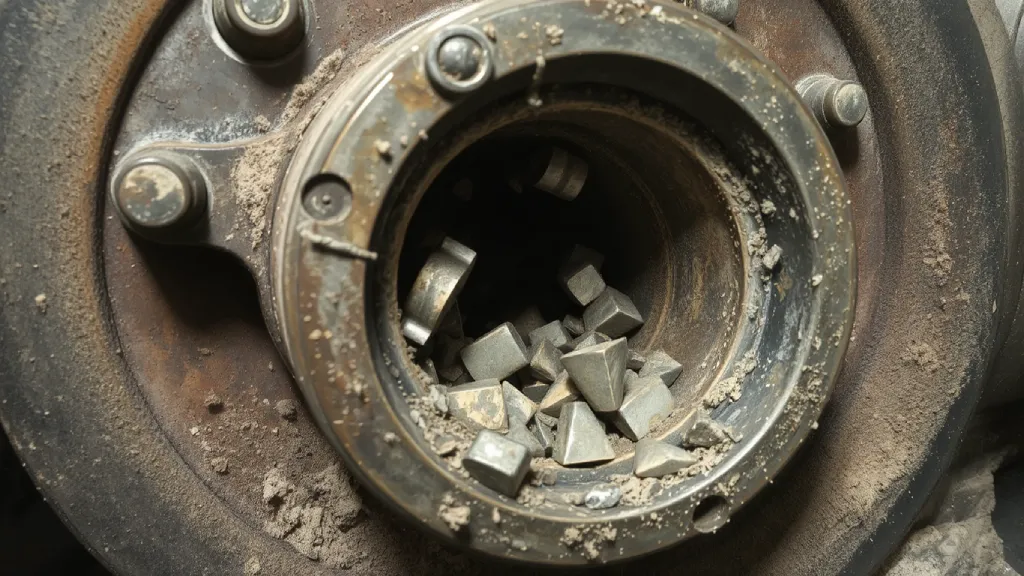
6. Power Loss or Fluctuations
Power loss or fluctuations can affect the ball mill’s performance, leading to inconsistent grinding results and potential damage to electrical components. Causes of power loss can include electrical faults, overloaded circuits, or improper voltage supply.
Solution: To address power loss issues, regularly inspect the electrical system and ensure that all connections are secure. Check the power supply for any irregularities or fluctuations, and address them accordingly. In the case of overloaded circuits, reduce the mill’s workload and distribute power demands evenly across the system.
7. Shortened Ball Mill Life Span
Ball mills are designed to last for many years, but without proper maintenance, their lifespan can be shortened. Common reasons for a shortened lifespan include inadequate lubrication, improper handling, and failure to perform regular maintenance.
Solution: To extend the lifespan of a ball mill, ensure that it is properly lubricated at regular intervals. Follow the manufacturer’s maintenance recommendations and perform periodic inspections to identify and address potential issues before they become serious problems. Train operators and maintenance personnel to handle the equipment carefully and perform necessary checks routinely.
8. Poor Product Quality
Poor product quality, such as inconsistent particle size or insufficiently ground material, can be the result of several factors, including incorrect mill speed, improper grinding media, or faulty mill operation.
Solution: Ensure that the mill is operating at the correct speed for the material being processed. Use the appropriate grinding media and adjust its size to suit the material. Regularly monitor the particle size distribution of the product and make adjustments to the milling process if necessary.
Conclusion
Troubleshooting ball mills requires a comprehensive understanding of their components and operational principles. Identifying the root cause of an issue and implementing the appropriate solution is essential to ensure the efficient and safe operation of the mill. By addressing common problems such as low grinding efficiency, overheating, excessive noise, and power fluctuations, operators can minimize downtime, reduce repair costs, and extend the life of the equipment. Regular maintenance, monitoring, and timely adjustments are key to maintaining optimal performance and achieving consistent product quality from your ball mill.
For more information on troubleshooting ball mills and finding the right grinding media solutions, you can contact Alpha Grinding Media. Their team of experts is available to provide tailored advice and support for optimizing your milling processes.
Frequently Asked Questions (FAQs)
1. What causes low grinding efficiency in a ball mill?
Low grinding efficiency can be caused by various factors, including clogged feed material, incorrect ball size, improper mill speed, or a lack of proper lubrication. Ensuring clean, dry feed material, using the correct ball size, and adjusting the mill speed to match the material being processed can help resolve this issue.
2. How can overheating of a ball mill be prevented?
Overheating in a ball mill can be prevented by ensuring proper ventilation, maintaining an appropriate load, and providing adequate lubrication to the bearings and moving parts. Cooling systems should be in place to dissipate the heat generated during grinding. Regular checks on the lubrication system and component conditions are essential to avoid overheating.
3. Why is there excessive noise or vibration in my ball mill?
Excessive noise or vibration can indicate issues such as worn-out bearings, misalignment of components, or an imbalance in the grinding media. If you hear unusual noises or notice vibrations, shut down the mill and inspect it for damaged components, alignment issues, or uneven distribution of the grinding media. Corrective measures should be taken to address these problems.
4. How can I prevent ball mill jamming or blockages?
Ball mill jamming or blockage can occur due to material buildup, improper feed rates, or incorrect mill speed. To prevent jamming, clean the mill regularly and ensure the feeding system is functioning correctly. Avoid overloading the mill and monitor the material flow rate to maintain smooth operation. In case of blockage, stop the mill immediately, clear the obstruction, and restart it after ensuring proper flow.