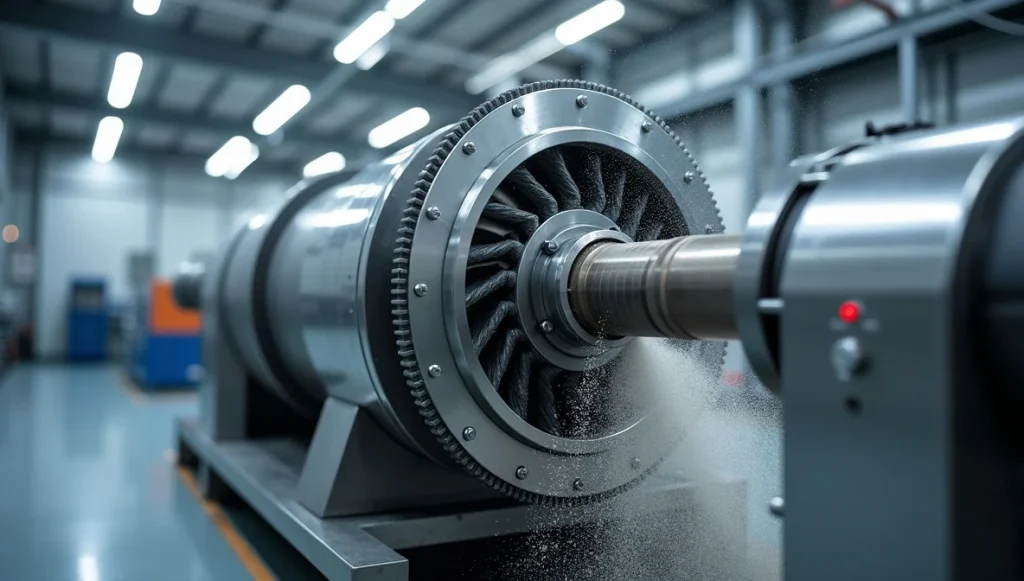
ALPHA GRINDING MEDIA
Established in Turkey, Alpha Grinding Media operates internationally. In just a few years, we have introduced ourselves as one of the most reliable grinding media suppliers. We try to back customers with excellence in products and services. Our grinding steel balls and rods are of the best industrial practices. That’s our policy to keep our customers happy in the long run! Alpha’s operations are supported by a team of young yet experienced specialists who are ambitious to increase its market share among other grinding media suppliers.
Many individuals are acquainted with the conventional milling machines that stand upright and feature rotating blades. Manufacturers commonly utilize this traditional design to reshape items. In contrast, a ball mill is a type of milling equipment that employs balls to pulverize materials. Comprising a hollow cylinder, the ball mill rotates around either a horizontal or vertical axis. This cylinder is filled with balls. As materials intended for crushing are introduced, the balls traverse the interior of the mill, impacting the materials.
Application of mill balls
Balls for ballmills serve the purpose of pulverizing materials into fine powders. They are employed in blending various substances, including chemicals, paints, ceramics, and minerals. Grinding balls, crafted from diverse materials such as stainless steel and ceramics, can be utilized interchangeably in similar applications.
To ensure the ball mill operates correctly, it must attain the critical speed. This is the velocity at which the grinding balls commence their rotation along the inner walls of the ball mills. Without reaching this critical speed, the grinding balls will remain stationary at the bottom and fail to grind the materials effectively.
Grinding balls are instrumental in grinding or blending materials. They function based on the principles of impact and attrition. Historically, these balls were crafted from steel, ceramics, or rubber. Nowadays, they are produced with a scientific approach, and Magotteaux manufactures them using alloys specifically designed for their intended tasks, resulting in reduced wear and significantly enhanced production efficiency. Guidance is provided on selecting the optimal balls for specific requirements.
In selecting a grinding ball or other grinding media, adopting a “Less is more” strategy is advisable. The optimal approach is to choose the grinding ball (or grinding rod) with the smallest diameter that can still effectively pulverize the material.
Exercise caution when selecting the size of the grinding balls. If they are too diminutive, there’s a risk they might be expelled from the mill with the waste material. Utilizing a grate discharge mill can mitigate this hazard.
For the initial stage of grinding, opt for larger grinding balls, typically sizes between 4”-2”. Certain applications may necessitate the use of 5” grinding balls at the outset.
During the secondary stage, where finer grinding is required, start with a smaller grinding ball, approximately 3” in size, and progressively decrease the size. For ultra-fine grinding, grinding balls of 1/5” or smaller are utilize.
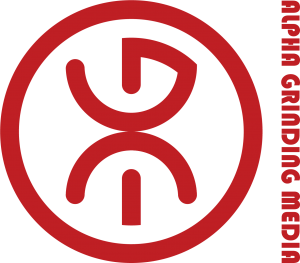